Why Strainlabs
Monitoring of bolted joints for optimal performance
- Short term to ensure correct installation.
- Long term to ensure proper maintenance and avoid failure.
- Collect data to be used for bolted joint design and dimensioning.
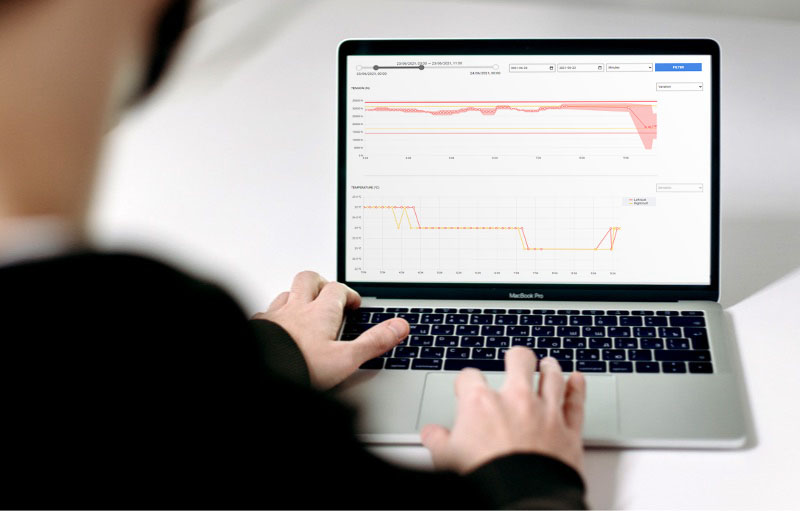
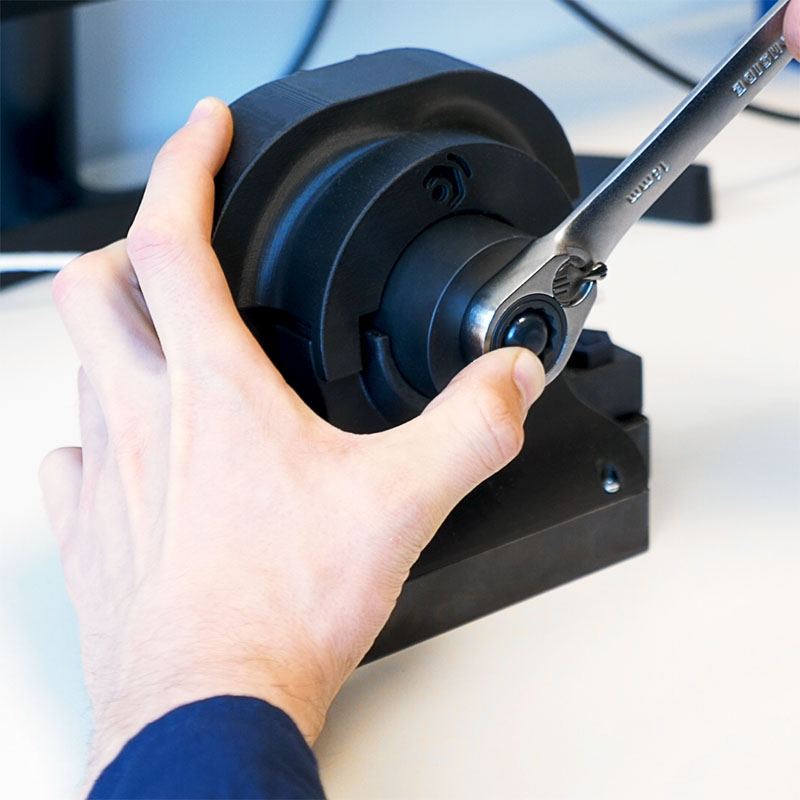
A Complete monitoring system
Strainlabs sophisticated solution includes bolts with patented LED sensors that communicate via a router to Strainlabs Analytics.
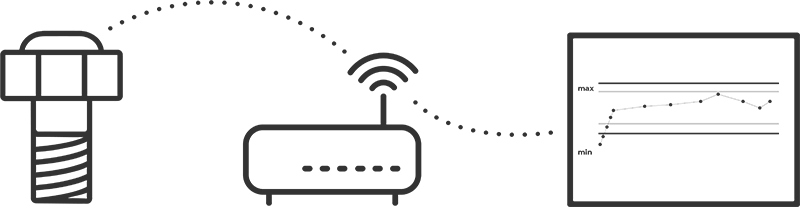
Unique & patented solution
- Strainlabs Bolts Connect an unlimited amount of preload sensing IoT bolts using patented LED-sensor technology to measure preload.
- Strainlabs Routers Pre-configured routers to receive and upload data results from Strainlabs Bolts to Strainlabs Analytics.
- Strainlabs Analytics Enables remote monitoring and alerts for Strainlabs Bolts. Aggregates quantifiable and actionable data.
Problems with bolts
A bolt can be associated with many problems, which a monitoring system can detect and provide notifications for.
Over tightening
The bolt is over-stressed and may break.
Under tightening
The bolt is too loosely assembled and cannot support its intended load.
Corrosion
Leads to microscopic cracks which ultimately fracture.
Leaking gaskets
If the bolts clamping a gasket are not evenly preloaded, the gasket will leak.
Fatigue
Too high cyclic loads induce fatigue and the bolt breaks.
Vibrations
Cause gradual loosening of the bolt and lead to failure.
Temperature effects
Fluctuating temperature expand and contract materials, which affects ‘the bolts performance.
Misalignment
Unevenly tightened bolts may cause mis- alignment and/or stress concentration of/in components.
Thread damage
Reduces the load carrying capacity of the bolt, which cannot support its intended load
Insufficient preload
The bolt is not able to withstand the working load it is intended for and will fail.
Business related consequences of bolt failure
If a problem occurs with a bolt and it fails, it does not only affect the bolt, but also the application which components it joins as well as the value chain which the application is a part of. Therefore, it is of high financial and operational value to any OEM and End-User organization to be notified about an upcoming failure and being able to prevent it from ever occurring.
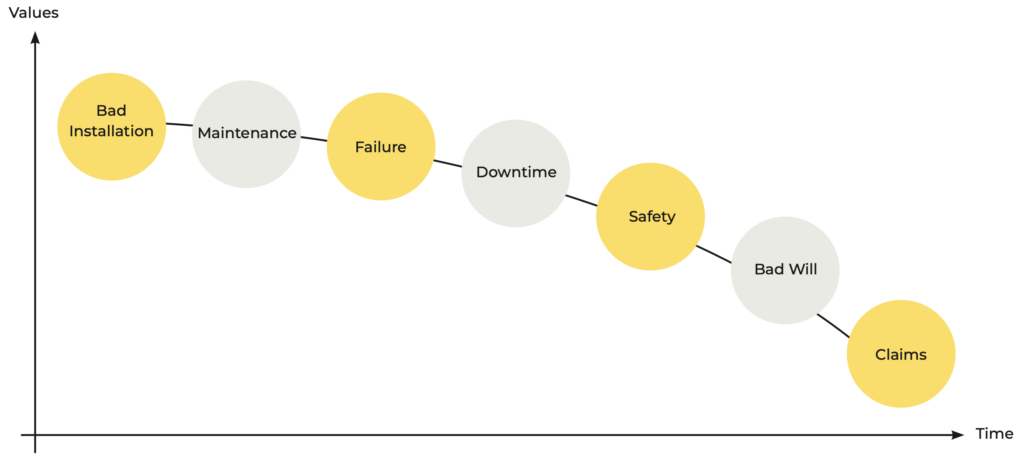
Such as down time, delivery delays and increased costs.
Such as revenue loss due to lost production, repair and replacement costs and machinery or parts thereof, fines for non-compliance with agreements.
Such as loss of credibility.
Such as danger to employees and equipment users as well as environmental impact.
Such as disruption of contractual obligations and regulatory compliance.
Such as competing with subpar products that fail.
Value for OEM
Such as revenue loss due to lost production, repair and replacement costs and machinery or parts thereof, fines for non-compliance with agreements.
Roller coaster manufacturer
Roller coasters and amusement park rides have an extensive use of bolts which must be regularly inspected and documented for customer safety.
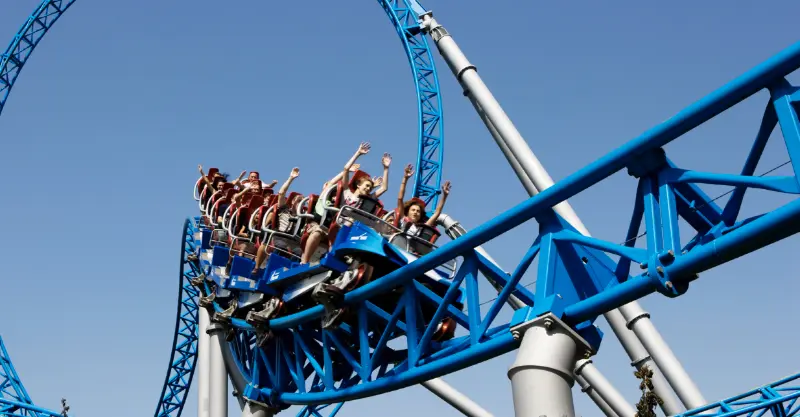
Selling data, such as raw data or analytical models, can be a new revenue stream beyond just selling physical products.
Data can provide insights into how customers are using their applications. OEMs can use this to create additional offerings.
Aggregated data from multiple applications can be used to identify trends and market opportunities.
The analysis of bolt data can identify application issues, predict maintenance needs, and be used to develop better applications.
Data can be used to identify future need and sellable features.
Improvements of products, processes and quality.
Value for End-User
The operational value of bolt monitoring is high for an End-User because it minimizes disruptions in business operational processes. Operations is the continuously improving process of producing goods or services which delivers value to the customer and revenue to the End-User in a sustainable way.
Paper mill / Rollers
The bolts retaining the rollers are difficult to tighten and sufficient preload is not always achieved.
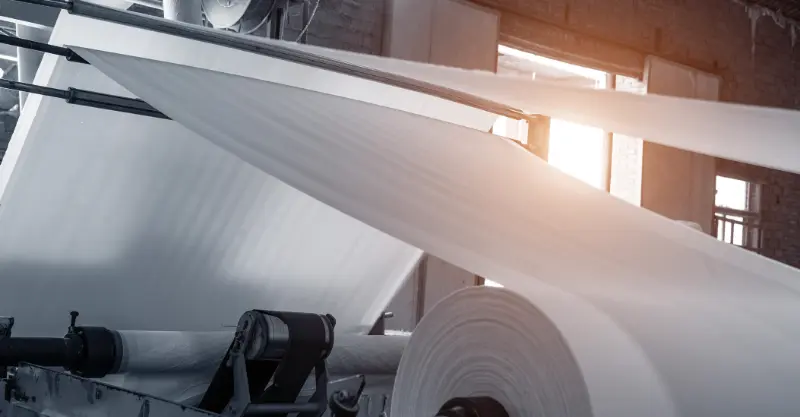
Can be increased when manual inspection of bolted applications is automated. Time is saved and documentation is automatically processed.
Automated inspections cut unnecessary expenses for tools, labor, down-time and value for lost production.
Failed bolts is one of the most common root causes for breakdown, which often leads to dangerous or environmentally hazardous scenarios.
Up-to-date, aware and well-trained employees are motivated, productive and con- tribute to operational success.
Every performed task leaves an environmental footprint. Automatic bolt inspection reduces the number of tasks performed and increase positive public perception.
Bolt monitoring can enable data-driven decision making, predictive maintenance and process optimization.
Knowledge hUb
Related Articles
When and where is it relevant to implement Strainlabs System?
Due to the wide use of bolted joints across industries, Strainlabs can provide valuable & actionable data to virtually any business, process or asset.