How long time does it take to inspect or (re)tighten a bolted joint? Multiply that with amount of bolts, the labor cost & how often maintenance is sought to happen – and you have the available cost, right? Well actually it is not all that simple if you want to get an overview and understanding for how digitalizing maintenance methods affects total cost of ownership. The following parameters affect the cost of bolt inspection or retightening activities and should also be accounted for:
- All onsite work must be planned, evaluated and authorized by management. Often climbing or hard to reach areas are involved. Additionally, it is not uncommon that extreme temperatures, electricity, or hazardous substances / gases are part of the on-site reality. The process and risks involved must be documented and reported beforehand.
- Machine stoppage (including cost for production loss) must be planned and for critical industrial areas need to be sealed off – often adding additional procedures to even get to the machinery / joint.
- A guard and additional people with special safety equipment needs to be on site throughout the procedure.
- The involved procedures require people with specific education / skill-sets / certificates.
This means that the larger cost drivers and resources needed to perform a bolt inspection or maintenance job in critical industrial areas are often not related to the actual tightening / untightening activity.
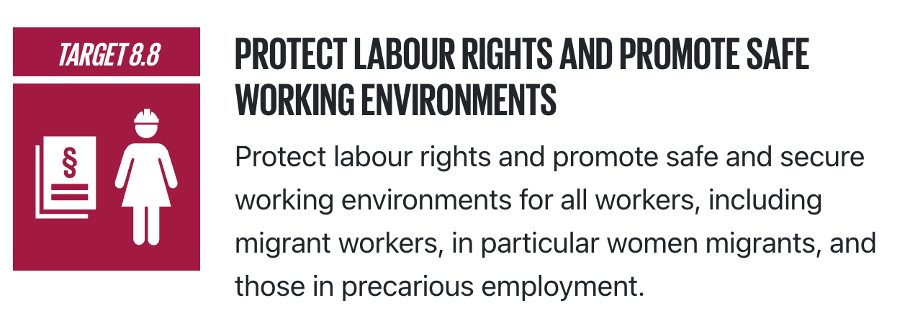
Traditional maintenance vs digitalization
Using Sweden as an example, a country generally considered to have high safety standards. Yet approx. 40 fatal accidents and 400 accidents leading to injuries has happened yearly during the last decade (Source: Arbetsmiljöverket). Most incidents are personell falling from elevated positions or dropped objects, and are a direct result of performing such tasks. All large companies are aware of these risks and in Sweden an organization called Standard Solutions Group (SSG) has been founded to draw up the necessary safety educations and routines required in order to increase safety and is in many cases required even to be on site let alone to perform a task. Similar initiatives exist in other countries as this approach is globally applicable.
Although bolted joint inspection or retightening of bolts is a common reason for maintenance teams to visit restricted areas, the general impression at management level is that bolts represent an insignificant cost related to cost of ownership. Adding the total risks of bringing personnel out to the equipment should be a valid argument to investigate alternative measures. Switching to predictive maintenance eliminates a large part of the risks, cost, and time at equipment by providing a remote and automated process for regular bolt inspection.
Strainlabs IoT bolts can greatly reduce the number of times personnel has to be put at risk, directly affecting Target 8.8 as part of the Sustainable Development Goals. Industrial companies should account for both the value of reducing risks and exposure as well of the actual total costs for performing each on-site job. Contact us to learn more about gains and how industrial digitalisation of bolted joints can enable more sustainable operations.