This article is a translation of an original piece published by Byggnadsarbetaren on August 8, 2024, which explores how sensor-equipped bolts developed by Strainlabs AB could have prevented the tragic elevator accident in Ursvik, Sweden. The original article discusses the findings from the accident investigation and the potential for innovative technology to enhance safety in construction. You can read the original article here (in Swedish).
How the elevator accident could have been prevented: “Would have detected missing bolts”
Sensor-equipped bolts could have prevented the elevator accident in Ursvik, Sweden, according to Csaba Madru, CEO of Strainlabs AB a company that has developed traceable bolts for bolted joint assembly.
Published in: Byggnadsarbetaren, Workshop safety on August 8, 2024
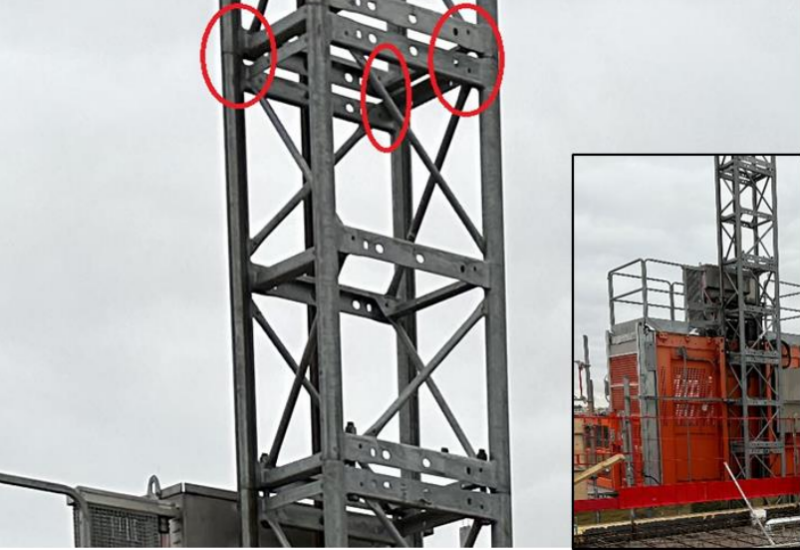
Five construction workers died when the elevator in Ursvik collapsed in December last year. It was later confirmed that four bolts were missing in a bolted joint between two sections of the elevator mast. The elevator had been traveling over this dangerous gap for several weeks before the collapse occurred.
Later, it was also discovered that an additional bolt was missing in another section, but this did not have the same catastrophic impact.
The accident should not have been possible to occur. Missing bolts should have been detected during checks of the elevator and the work. The accident investigation commission assumes that the bolts were missing during the assembly of the critical sections on November 1. It remains unclear whether the bolts were missing during transportation from the rental company’s premises or if they were removed from the mast section before assembly.
Since then, bolts have been painted with contrasting colors to ensure any issues are immediately noticed.
“Missing bolts would have been detected”
However, Csaba Madru with Strainlabs AB believe they have the products and technology that could have prevented the Ursvik accident and could make many machines, such as elevators, safer.
Could your system have prevented the accident?
– “Yes, the missing bolts would have been detected. This is exactly the kind of accident we aim to prevent.”
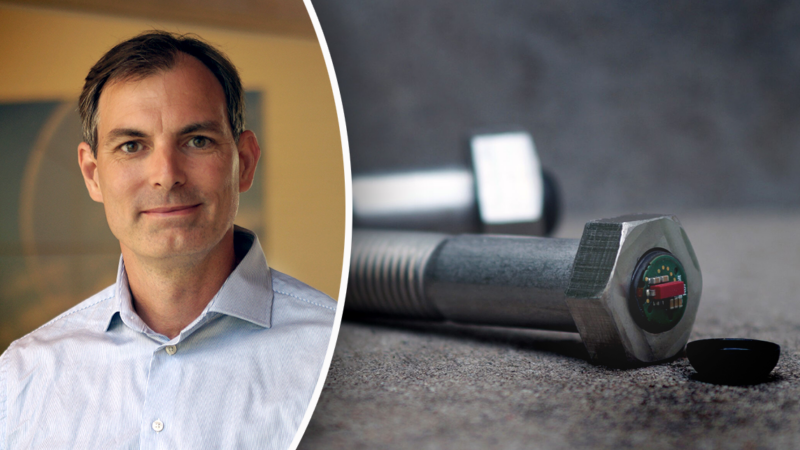
The bolts and technology have been on the market for about two years. The company was founded in 2014, but the technology did not exist at that time.
The product consists of three parts:
- A bolt with integrated sensor that reacts to pre-load, the force generated in the assembly when bolted joints are tightened.
- An internet gateway with multiple functions. It receives data from the bolt(s) at predetermined intervals and then sends it to…
- A cloud service where all data is processed and analyzed. The system provides automatic alerts for pre-load, temperatures and other factors affects the desired pre-load range specified by the customer.
How is the bolt data monitored?
“You can be anywhere in the world, and the system is designed so that each bolt has a unique ID, allowing you to locate the exact position of each bolt within the bolted joint. If you have a joint or machine with for example one hundred bolts, you can know exactly which one of those has an issue,” says Csaba Madru.
Ensuring correct assembly
With the company’s software, you can monitor how each individual bolt behaves. You can access the application via phone, tablet, computer, etc. When the parts and bolts are assembled in the construction for the first time, there is a mode called real-time (with a one-second delay) where you can ensure everything is assembled correctly. Once assembly is complete, the real-time function shuts off, and the system follows up with updates every ten minutes to check how the bolts are performing. The system alerts you to any issues.
The ill-fated elevator in Ursvik was owned by the elevator manufacturer Alimak. Strainlabs has been in contact with them several times, both last fall and this year, before the accident.
– “Their interest has been limited” Csaba Madru notes.
Is there a significant cost difference?
“Typically, a bolt costs around 100-200 SEK. For an elevator, I estimate the price to be around 1,500 SEK for a single bolt, but when purchasing multiple, the cost drops significantly. We calculated that the cost could be around 30-50 SEK per day for an elevator. When it comes to personal safety, the price becomes a non-issue.”
According to Csaba Madru, operational disruptions due to assembly issues often incur significant costs. This is also the main cause of most safety problems.
Another reason for issues with bolts is natural wear over time and work, which causes the material to settle.
Today, Strainlabs Bolts are used on railways, in railway switches, in paper mills, and in the mining industry for example.
Colored bolts
According to the Swedish Accident Investigation Authority, Alimak has implemented several measures after the accident. Among other things, they have developed colored bolts for the mast. Visual plastic indicators have also been introduced to make it easier to check that the nut is in place. Digital tools have been developed to calculate installation more easily and safely during inspections, and to verify whether daily inspections have been carried out according to the manual.
But what does Alimak say about Strainlabs’ sensor-equipped bolts? Johnny Nylund, press officer at Alimak Group, responds via email: “We continuously evaluate solutions as part of our product improvements. However, we do not comment on specific products/solutions we are evaluating if we have not decided to implement them in our products yet. A key aspect is the human factor and ensuring that the bolts are correctly installed. For this purpose, we have introduced colored bolts and nut indicators as a first step. But of course, we continue to work on this issue, and we will contribute in every way we can to improving overall workplace safety.”
Join the Facebook group “Workplace Safety in Construction” and get the latest news in your feed.
Original article written in Swedish for Byggnadsarbetaren (The Construction worker) by
Margite Fransson, Reporter
mf@byggarb.se