Floating solar installations located in dams or coastal areas are becoming more prevalent, with structures commonly around 60,000 square meters (200 x 300 m²), project capacities spanning from 5 MW to more than 100s of MW. These installations are highly desirable as they produce renewable energy with minimal visual impact. However, inadequate anchoring, or mooring, of these large structures poses significant risks, which have historically led to costly and dangerous failures, including potential environmental damage.
With over 40 years of experience and more than 2,000 installations worldwide, Seaflex is a leader in marine mooring, securing everything from small harbors to large floating structures at sea. Since 2011, Seaflex has increasingly focused on floating solar panels, working to innovate in this area by ensuring that these structures are securely moored and efficiently monitored. The complex nature of floating solar installations requires a large number of attachment points and careful load calculations to ensure stability. Despite these efforts, traditional methods still require frequent manual inspections in accessible under often harsh weather conditions. This can lead to unnoticed wear and potential detachment from moorings.
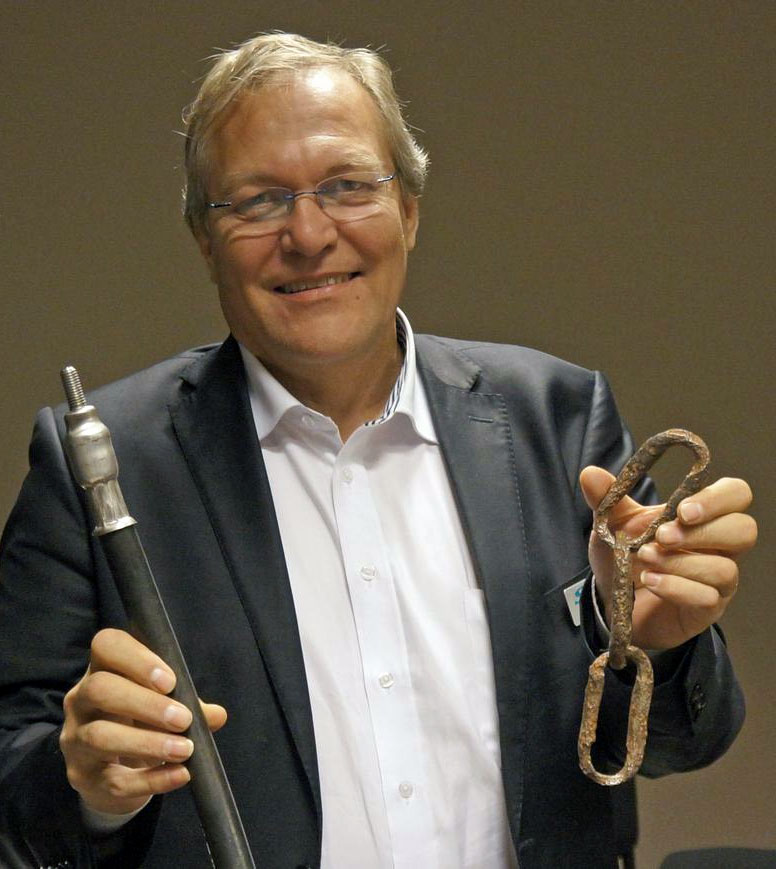
Lars Brandt, CEO of Seaflex explains: “The industry is in great need of a reliable way to monitor the security of these structures, with an alarm feature to alert us when there’s a risk of loosening.”
Image: Svenskt näringsliv
The inadequacy of traditional solution: The load cell
The industry and well known standardization body DNV is working on establishing a standardized methodology for calculating and handling loads in the mooring of floating solar structures. Traditionally, load cells have been the go-to technical solution for monitoring these loads. However, load cells are not only expensive (costing around USD 2.000 per unit), but they are also impractical in marine environments. Saltwater and pressure can compromise the functionality of the cables and sensitive electronics involved.
Application with load monitoring requirements
In one project, a floating solar panel installation measuring 300 x 200 meters was secured with 20 anchor points, with four ropes at each point. Involved is the project owner EDP. Regulatory entities has also asked for the monitoring of the loads on the moorings, which this solution now can solve. However, the number of load cells needed made the project economically unfeasible. Despite support from RISE (Research Institutes of Sweden) and best-practice installation methods, the technical requirements could not be fully met.
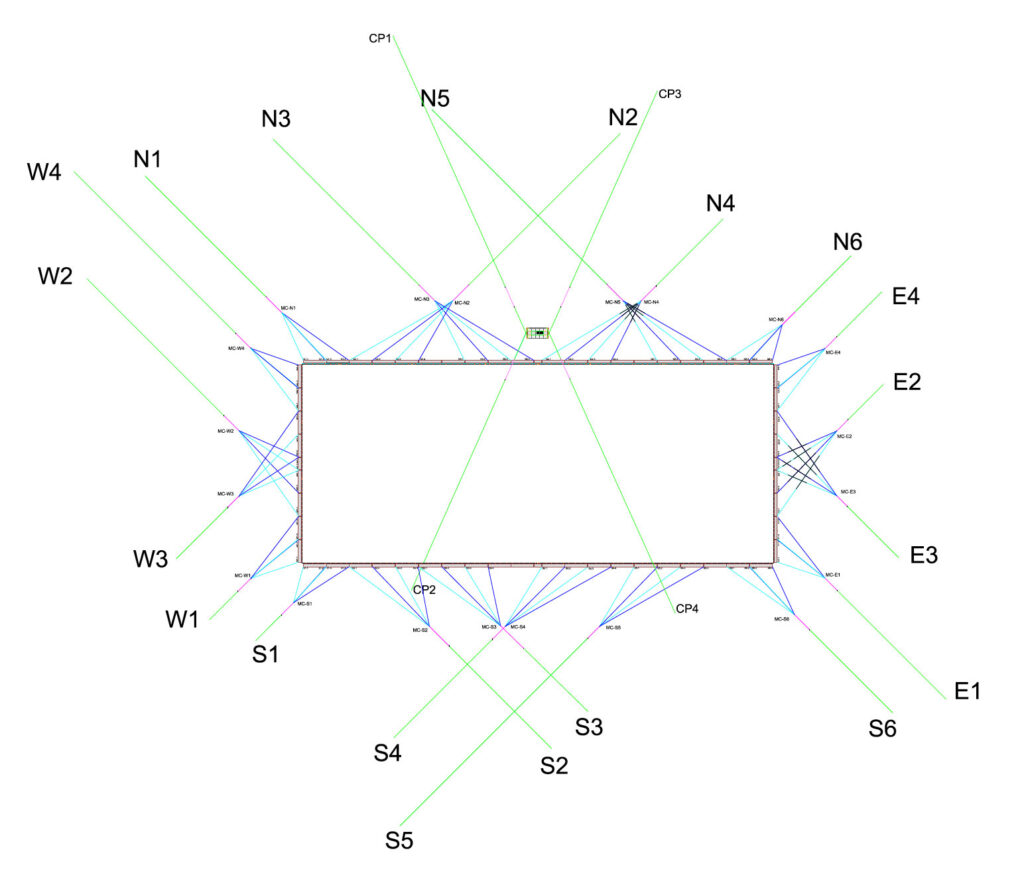
Innovative partnership for a long-term solution
Seaflex and Strainlabs are closely collaborating to develop what could become a new industry standard for monitoring the mooring of floating solar panels. The teams are working on mutual design efforts to integrate Strainlabs’ technology into existing mooring solutions, ensuring the best possible outcomes during the validation phase.
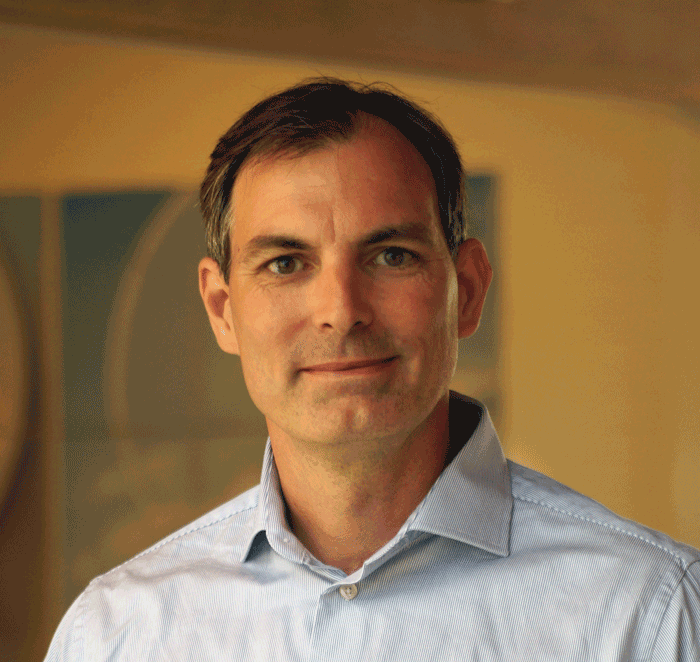
“Together with Seaflex we are looking into the best way to transfer the load from rope to Strainlabs Bolts as well as the optimal design to ensure stable communication from the bolts to Strainlabs Analytics under the specific environmental and structural circumstances” says Csaba Madru, CEO of Strainlabs.
The long-term ambition of Seaflex and Strainlabs is to establish a technically and economically superior standard for moorings monitoring. Lars Brandt adds, “Incorporating Strainlabs into our mooring solutions will not only improve the safety and security of floating structures but also enable more efficient and sustainable maintenance methods.”