The Øresund Bridge is known for its work on a digital twin, developed for the 16-kilometer long connection. The digital journey started in 2018 in a collaboration with Afry. Since then, the work with the digital twin has been refined, with more assets and functions added each year. The conditions of the facility are captured in a digital visualization tool, enabling large parts of the maintenance and project planning to occur from the office.
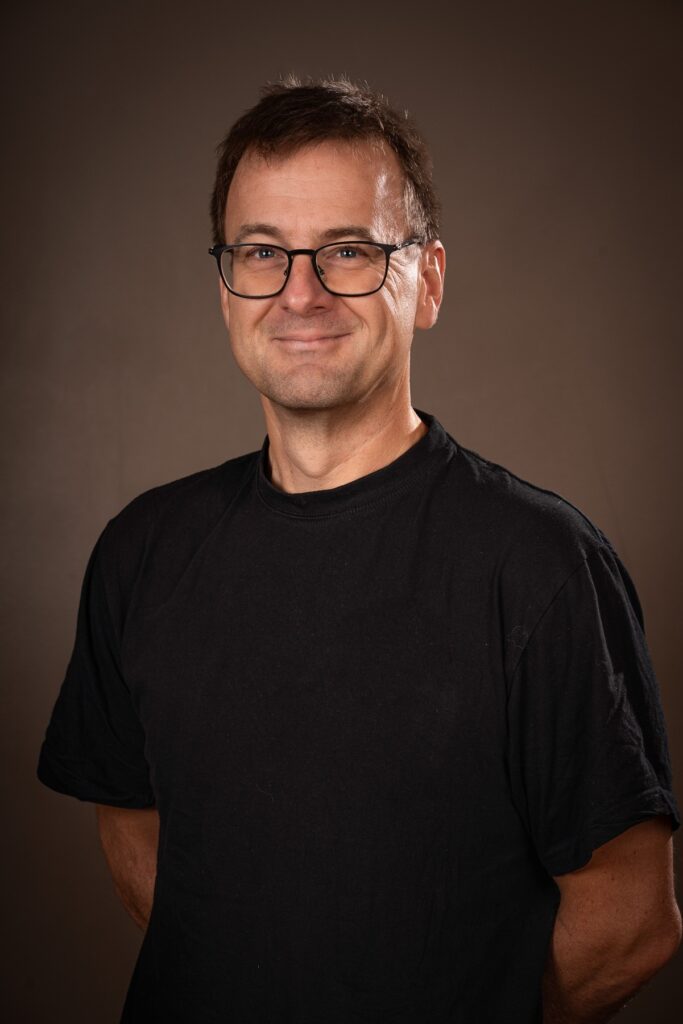
“We aim for the most data-driven and smart maintenance possible, and we have an ambition for the facility to notify us when it needs attention. The bridge is designed to last 200 years – we have 175 years left, and we are already looking ahead to what will happen further down the road. We don’t wait for needs to arise; instead, we work proactively towards more AI and machine learning. We want to move away from traditional calendar-based maintenance, which is why this is an interesting pilot project” says Andreas Jälmarstål, technical manager, railway at Øresundsbron.
Application installed on the tracks
The pilot application involves monitoring of so-called particle magnets, a technique that helps prevent issues caused by iron dust formed when trains brake and roll over track insulators. The magnets effectively collect iron dust and prevent the formation of unwanted “cakes” of iron dust that could otherwise cause short circuits in the track circuits, leading to delays and other operational disruptions. The pilot project between Öresund bridge and Strainlabs progressed quickly, as the team was already well aware of the value of monitoring preload in bolted joints.
Pekka Öhrstedt, steel and concrete specialist at Øresundsbro Konsortiet, explains:
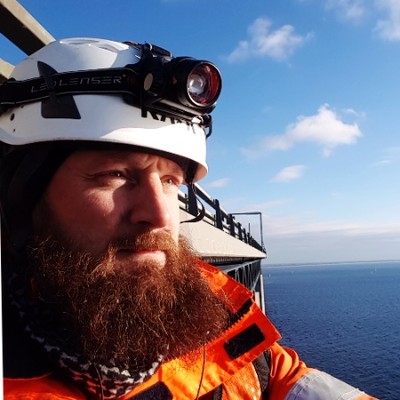
“It doesn’t matter much if we go around and manually inspect bolted joints – to ensure a secure installation, we need information about the actual preload over time, not just a snapshot of information at tightening.” He continues: “We see several potential applications ahead, but we chose particle magnets as the first asset to apply the pilot to. Knowing for sure that these magnets are in place plays an important role in avoiding traffic stoppages, and the installation was relatively accessible from Peberholm.”
The challenge
Inspection of particle magnets currently requires physical presence on-site, which is resource-intensive. Without monitoring the bolts that fasten the magnets, it is difficult to know when a magnet starts to loosen and risks detaching from its position. This is especially challenging due to the long stretches of continuously trafficked railway. This pilot project is part of a larger ambition to transition to safer and more data-driven work methods, aiming to reduce the need for physical presence at the facility – particularly for critical and hard-to-reach bolted joints.
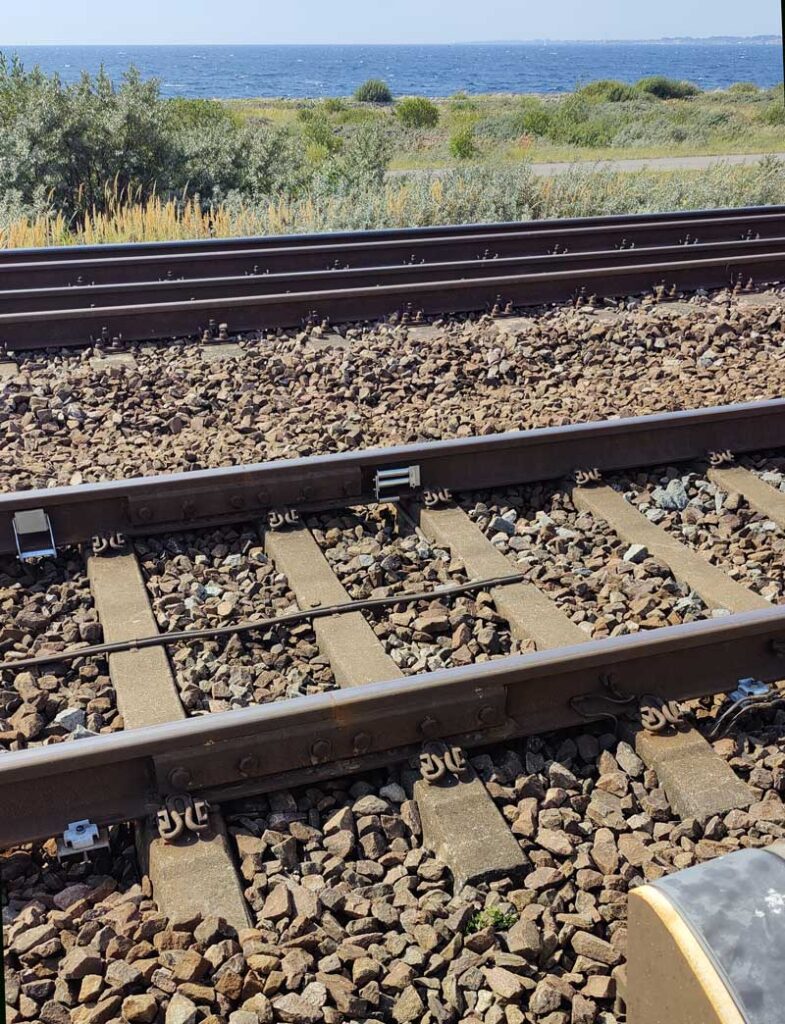
The implementation
Csaba Madru, CEO of Strainlabs, comments on the collaboration: “Øresundsbron is extremely competent and has a clear plan for how to future-proof its operations. It has been very easy to collaborate with them and move from theory to practice in a short time. This pilotproject is a first step, and we are learning a lot about how maintenance digitalization should be implemented to maximize value.”
Strainlabs’ solution includes:
- Strainlabs Bolts (16 pcs M10x80, Bumax 88 bolts) that mount several particle magnets along the tracks on the Øresund Bridge.
- Strainlabs Router with signal amplifier: The installation of a router with dual concentrator cards for antennas, directed in two different directions, has been completed at Peberholm.
- Strainlabs Analytics: Software that is part of Strainlabs System, providing real-time data during installation and long-term monitoring of the bolted joints.
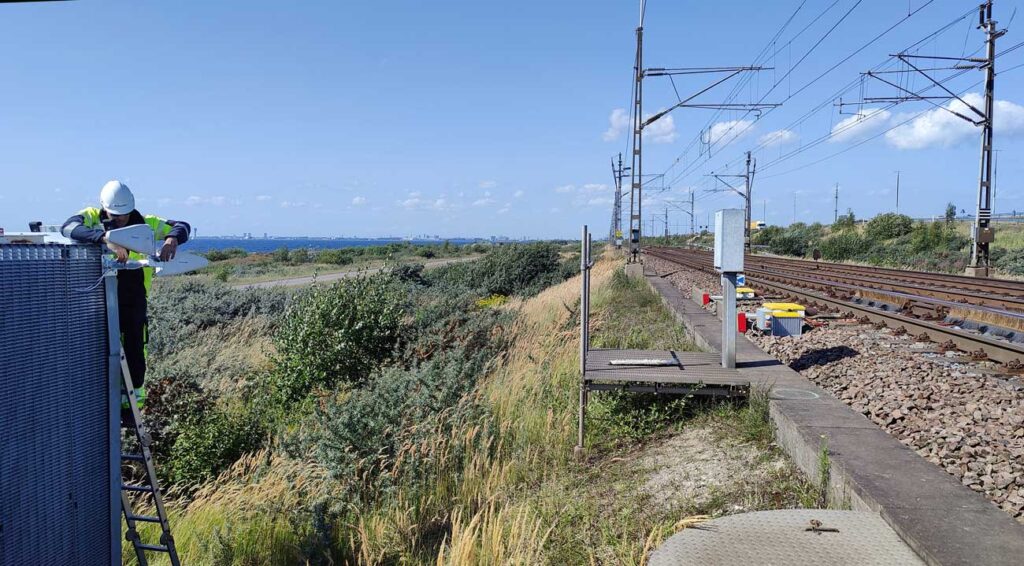
The potential
“By automating the monitoring of the particle magnets, Øresundsbron can, with Strainlabs’ system, ensure that the bolts are correctly installed with the proper preload from the start. Our product makes it possible for our customers to track and analyze how the preload changes over time, despite fewer physical inspections. This in turn, allows maintenance work to be smarter planned, prevent operational disruptions, and further improve the related routines,” adds Csaba Madru.
“There are many bolts installed on the facility – not just railway applications but also large structures, bridge bearings, underground pumps, and more – connections constantly exposed to vibrations, weather, and wind. This is an important evaluation step of how reliable the data is and we look forward to following this pilot. We are open to testing new innovations on our facility, which, in our experience, often results in a win-win,” concludes Andreas Jälmarstål.