Boliden has a long tradition of pioneering digitalization and testing new technologies to modernize and automate work within the mining industry. By actively investing in predictive maintenance, the company aims to minimize unplanned downtime and maximize safety in its mines. As part of this strategy, Boliden is now evaluating Strainlabs System in two critical areas of the production flow: a stationary jaw crusher and an underground loader.
“Our unit drives maintenance improvements and helps implement new technologies we believe add value across all Boliden sites. We now have two Strainlabs applications running in Garpenberg. One is on the jaw crusher, where it’s extremely difficult to inspect or even detect if the bolts are loose – we want that data-driven. The other application is mobile – a rotating shaft on a vehicle that moves around. Our underground machines have good connectivity, and we want to explore how we can integrate bolting data with other data sources to gain an even deeper understanding of our equipment and its condition.”
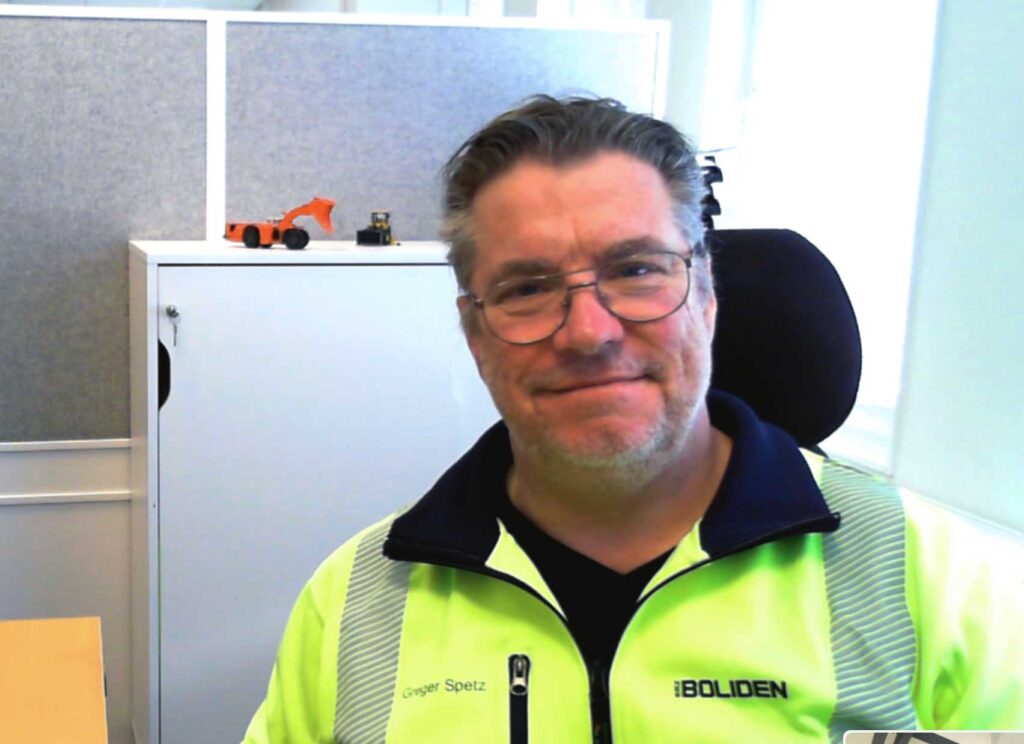
Greger Spetz
Maintenance Technical Manager,
Boliden Mines
Strainlabs installed for monitoring of jaw crusher
One of Boliden’s most critical production units is the jaw crusher, used to crush ore. The bolted joints here are exposed to intense vibration and impact loads, which can cause loosening and, in the worst case, production stoppages. To reduce the risk of unplanned downtime, Strainlabs Bolts have been installed at several strategic fastening points (M36 bolts), securing the steel plates that process the ore.
Previous unplanned stops have led to significant production losses, both in terms of downtime and necessary repairs. Boliden is now evaluating Strainlabs technology as a means to predict maintenance needs.
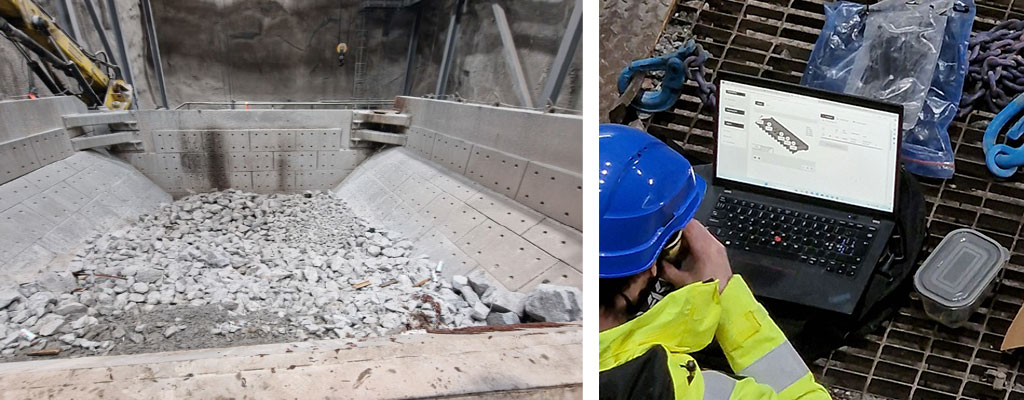
Strainlabs CEO Csaba Madru comments:
“Boliden is a role model in driving digitalization and sustainability within the mining industry. This implementation is a major step forward in realizing true predictive maintenance. Together with Boliden, we’ve also solved the challenge of monitoring bolted joints on mobile equipment, such as underground loaders – a real achievement by both teams in a very demanding environment.”
Strainlabs Bolts on an underground loader
Strainlabs Bolts have been installed on an underground loader – a vehicle subjected to extreme loads in Boliden’s mining operations. The bolts are positioned at nine locations along the drivetrain, including axles and mounting points. Loose bolts at these positions can lead to severe damage and, in worst case, require the vehicle to be towed or taken out of service.
To ensure stable connectivity, a Strainlabs Router has been integrated into the vehicle’s system by Boliden’s team. The bolts communicate wirelessly via this router, enabling remote monitoring of the application’s condition. This allows the maintenance team to act before a critical failure occurs.
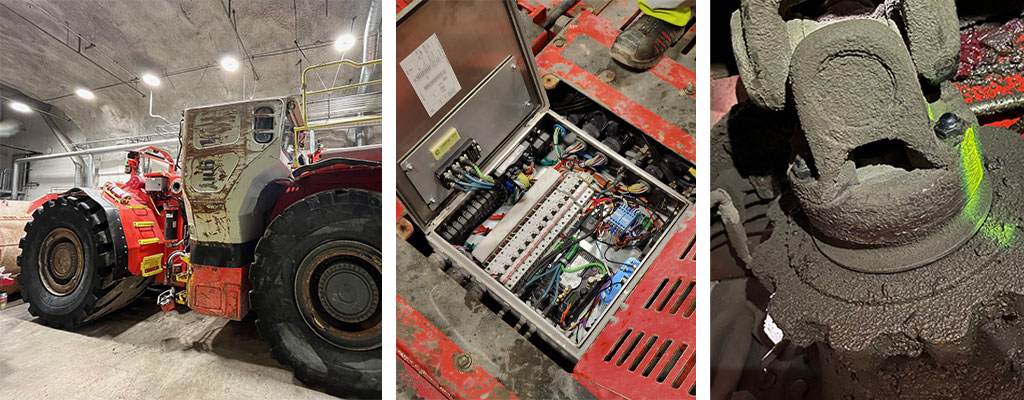
Results and future potential
The implementation of the Strainlabs System is currently being evaluated by Boliden’s central maintenance team. Digital maintenance is a key part of Boliden’s long-term strategy for increasing automation and enabling predictive operations. If the trials on the loader and crusher continue to deliver positive results, the technology could be deployed across Boliden’s mining operations.
Greger Spetz, Maintenance Technical Manager, Boliden Mines:
“The machines where we are testing Strainlabs System are extremely important – we don’t want any downtime on them. Just getting feedback on preload during tightening already adds value by securing quality in our work. We still have several steps left in our evaluation and learning journey about the insights this system can unlock – for instance, reduced manual inspection and how data can help us prioritize and respond faster. We’re not new to testing technologies, and it’s important for us to also explore how this data interacts with our other systems and models.”