Preload monitoring
Business Case
Opportunities with high impact
When maintenance is treated as a strategic function, it can have a substantial effect on reliability, profitability and efficiency.
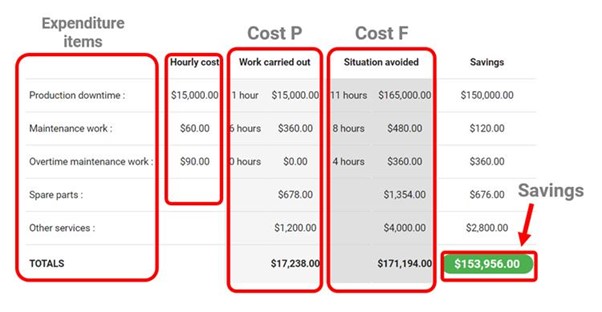
Example 1:
When you get to fix problems before failure occurs
Bolt preload is crucial for safety and function of industrial applications, and undetected bolts in a non-functional preload range can lead to functional failure. Reliable plant presents a pragmatic summary of how to calculate the benefit of avoiding a functional failure (Cost F) and fixing the problem when the issue is detected as a potentially upcoming failure (Cost P).
Figure: Repairs cost expenditure items, source: Reliable Plant Magazine. Repair costs at a Potential failure (P) will be relatively low compared to a Functional failure (F).
Note that the diagram only considers direct cost, potential related indirect or hidden costs are not mentioned in the table but would relate to production loss, quality issues, preventing risks, environmental and more.
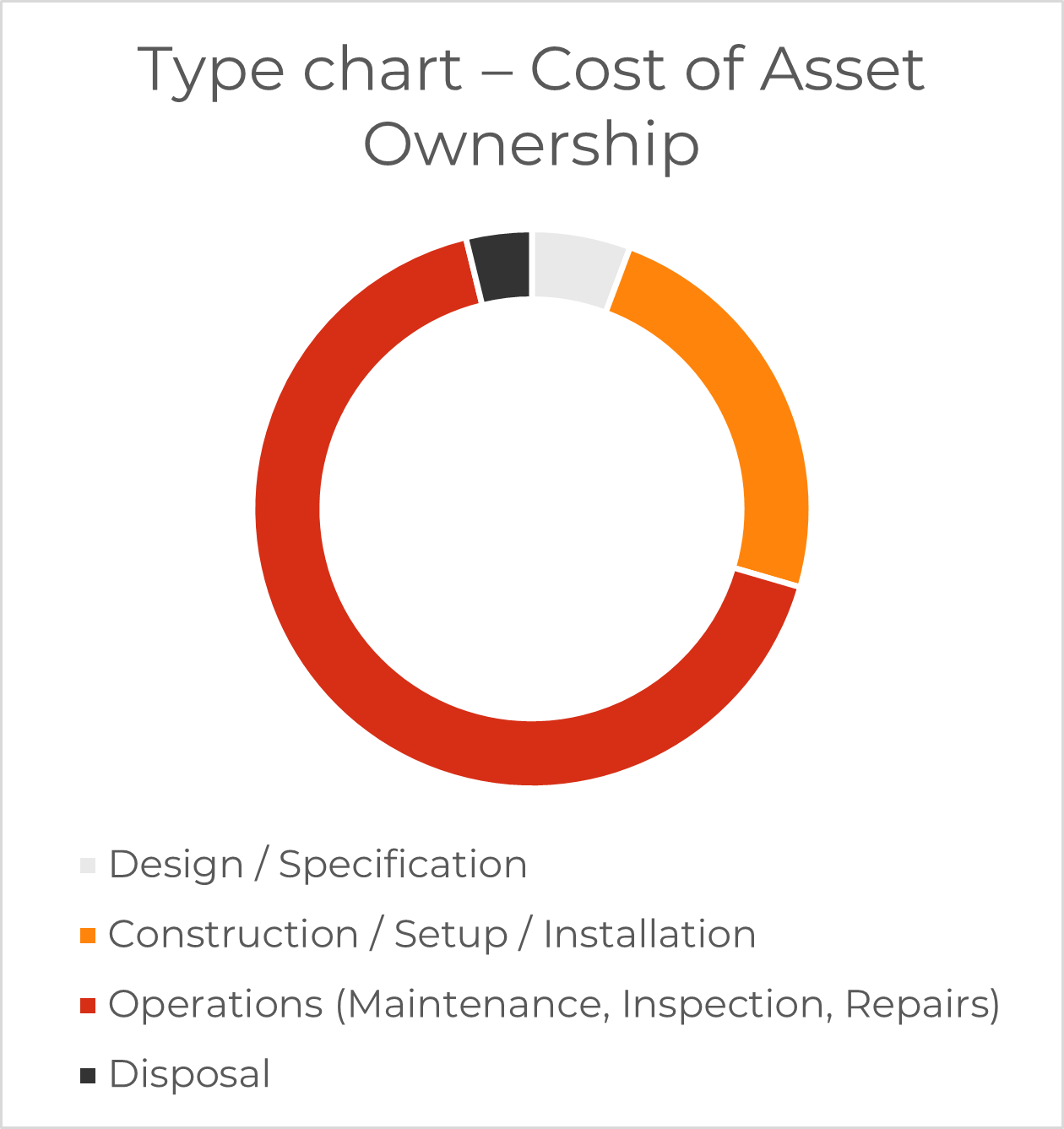
Example 2:
When inspection and maintenance accounts for high costs / risks
A robust predictive maintenance setup combines a maintenance team as well as diagnostics and condition monitoring. If your business and revenue depend on certain production assets, bottom lines are clearly affected by uptime. Condition monitoring can, besides detecting a failure before it happens, add both cost efficiency and frequency to the maintenance mix. Higher flexibility with more means for inspections is especially relevant for bolts that are hard to reach or in locations that exposes the team to safety risks. When reviewing cost of asset ownership, and the maintenance and inspection portion is a significant part of costs – considering preload monitoring becomes relevant.
Example 3:
When you want to remain the market leader
Getting the most from your asset / process gives market advantages, and data enables perfecting further on for example unexploited efficiency areas, ensure value and efficient problem solving as well as staying ahead as regulatory requirements change. Reliability in the core technique or offering is an increasing focus in particular Smart Manufacturing, sometimes called Reliability Cantered Maintenance (RCM). Asset management is seen as operations, not maintenance. For mechanical industrial structures, consider the value of bolt preload and further the risks of wrong preload – perhaps already at installation. What value would it mean if you for core processes / customer’s experienced clear reductions in for example:
- Downtime %
- Reactive maintenance %
- Incidents %
- Cost of inventory %
The options
Stay analogue:
There are some good methods for bolt securing mechanically and chemically to securing bolt from losing clamp lengths. Laboratory test shows efficiency however; those solutions will not inspect themselves, follow up on operator / tool accuracy and then risk not standing the test of time and environmental changes. They will not inspect themselves and your application, nor your maintenance processes, will get more digital.
Choose a “smart bolting” solution:
There are a range of bolt options that may categorize themselves as smart meaning attempting to offer bolt preload inspection externally (i.e. without untightening). Benchmarking questions we would recommend is if you actually get a relevant value as data tied to the position and time (for analysis), if you can inspect remotely or need to geographically be close to the bolt, if data is aggregated and offers alerts automatically. If it would be easy to test and implement as part of maintenance routine to drive better decisions. Strainlabs is the only complete IoT System on the market today.