Wireless communication is defined as sending data from A to B using electromagnetic waves with air, water or vacuum as a medium. In telecom, before wireless technology, cables were used as a medium. e.g. an old telephone switch where the operator manually changed the connections so the information could be transferred from A to B. In a modern world this would not be scalable with over 15 billion mobile phones (2021) and thus we interact daily with wireless devices.
The same goes for sensors, and since more and more devices are being connected to the internet Strainlabs IoT Bolts is part of an overall progression to remote proactive maintenance and new insights in bolted joints.
Key challenges with wireless sensors
To use radio communication in remote monitoring of bolted joints, key factors to overcome, include antenna development and integration, managing multiple sensors and Faraday’s cage.
Antenna development and integration
The antenna used in our sensor is custom made and operates on the same frequency as Bluetooth and Wi–Fi. The challenge of creating an antenna on limited space – our smallest bolt is M10 – demands experience to overcome. Prominent engineers helped design and test our antenna. The result is quite impressive taking into consideration that we have a battery powered sensor no larger than a standard shirt button sending data over 100 meters in Line-of-Sight Propagation.
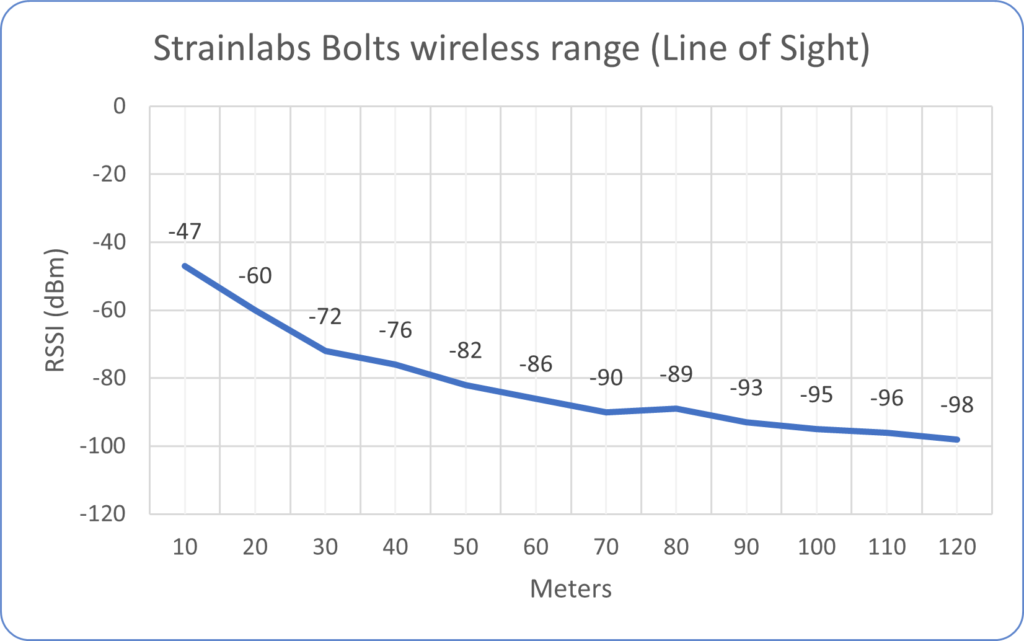
The graph above is measured with Strainlabs standard receiving antenna. The weakening of a signal is called attenuation. If a large distance is required, a directed antenna can be used to single out a bolt or a cluster of bolts to hone in on them, sort of like radio binoculars to put it simply.
Managing multiple sensors
The 2.4 GHz band is heavily operated with wireless devices on Bluetooth and Wi-Fi, therefore we operate on the part of the band with less traffic. Being on the 2.4 GHz band brings us the benefit of being able to integrate the antenna directly to the bolt. But also we can handle lots of bolts, up to 500 Bolts can be handled from one gateway as long as the internet connection is good. If the internet connection goes down, we still save data for when the gateway is online again.
Faradays Cage
Material such as steel can act as a Faraday’s cage since it is conductive, meaning the material can affect the electromagnetic wave we created containing our data. This brings a challenge to us as developers to overcome. And to top it off the environment most bolts are found in are heavy industrial facilities with machines and structures made out of steel.
Different materials have different attenuation coefficient, meaning they weaken and affect the signal differently. Materials such as wood, plastic and glass have a relatively low coefficient and doesn’t affect the signal much.
With Strainlabs System, several Strainlabs Routers can be used to ensure that signals from every bolt is received, and we also handle duplicate data. If more than one gateway receives the same radio package there will be no overlapping when data is presented.
Benefits of cutting the cables
The benefits of going wireless are many as we can tell from the progression of devices we use daily. In bolting and mechanical fastening there are equally many benefits from getting insights without worrying about cable management and charging.
Strainlabs System can easily be scaled and once you have adapted the system more sensorized bolts can be introduced easily. Just activate them in Strainlabs Analytics and install them to start monitoring preload.
The system has been designed to suit most industrial applications meaning the ability to be able to send packages of data as far as possible without consuming too much battery power. The bolts have one way communication for battery reasons and the gateway collects all packages that reaches it and sends it to the cloud.
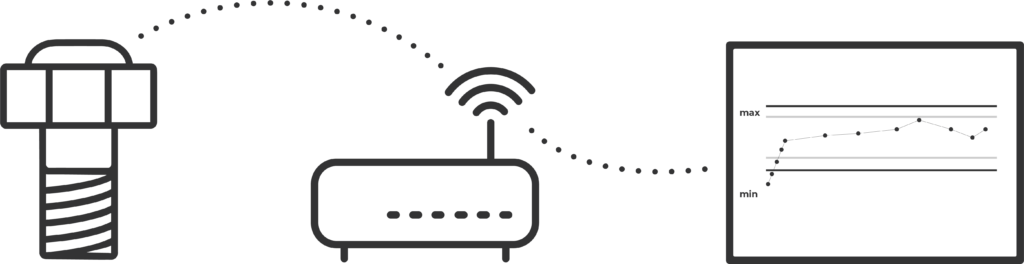
Along with IoT, automation is a big trend. PLCs (Programable Logic Controllers) are becoming more advanced and can benefit greatly from accessing wireless sensors. This means PLCs now have opportunity to halt a process before damage or faulty behaviour.