…That is true, until you put them together of course. Then you have a very different dynamic where the nut & bolt then behave much like a tension spring. In his professional carrier, Scott works with automotive OEMs assembly plants and is often called upon to undertake joint failure investigations to identify the failure mode attributes. He judges that 9/10 instances in industry are a result of not delivering enough clamp load meaning the input torque is more generalised and in many instances is incorrect. His experiences prompted him to highlight why bolt tension and not torque is the prime goal in safety critical applications and why he recently shared an article on LinkedIn that sparked quite some interest among bolting professionals. How do you know you develop enough clamp load? Scott Donnachie has become an advocate for focusing on the preload or clamp load achieved after hearing about and experiences many instances with incorrect application load due to a focus the erroneous belief that application torque is all that is needed to ensure a joint is correctly tightened. We invited him to the Internet of Bolts blog to explain more about his thoughts on the topic.
Why is torque input an insufficient focus for industrial bolting?
There are so many variables in a bolted joint that even two bolts from the same manufacturing batch will have different results when the same torque specification is applied in the same application. Here are some – just to name a few:
- Microscopic surface asperities (roughness)
- Minute dimensional differences in the bolt and internal thread itself
- Lubrication
- Different plating thicknesses
- Difference in localised coefficient of friction
- Depth of engaged thread
- Bearing surface area available
- Thread tolerances
- The tooling capability & accuracy
- Small variations in joint materials
- External loads acting on the joint
All of these elements, none of which can be statistically controlled to a finite degree, combine to affect on how much clamp load is ultimately generated in a bolted joint. Therefore, to think, or even expect that a given torque specification alone will consistently produce precise, repeatable & correct clamp load / preload results is not realistic.
Why is the focus on torque a problem on an industrial or even societal level?
Consequently, it is not uncommon to hear of joint failure in vehicles and other structures & assemblies – or the space shuttle incident I shared the article, to name a few. In some instances, joints with incorrect or insufficient torque lead to catastrophic failure and we have seen increases in the collapse of wind turbine generators due to bolt fatigue as a result of improper tightening and verification of such. You don’t have to look far to find these reports.
This is why I, both on a personal interest and a professional level started following and keeping track of solutions that has a potential to contribute to a change towards a focus away from torque since it does not deliver the clamp load that you need, it is not a reliable means to an end. In the industry I work in currently, automotive, there is enthusiasm, but also apprehension to adopt something new without lengthy and costly safety validations. Besides Strainlabs, I follow a few of the other companies that offer similar digitised bolting solutions where torque is no longer the focus. I haven’t done a thorough benchmarking analysis as yet, however all effectively measure bolt elongation as opposed to input torque as the end goal.
What I can say though is that I found the live demonstration that Strainlabs conducted over teams for me to be very interesting – especially seeing the analytics functionality. To be able to see, live, in-situ feedback, at a point at which the clamp load in a bolted joint, even among a series of joints, decreases, can be used in conjunction with other relative factors & failure investigation techniques to better pinpoint the root cause of the failure.
How would technologies that digitalize bolted joint can become relevant in your industry/field?
The focus would not be to leave such technology on a vehicle indefinitely, which is the case for most other structural fasteners. Where I see a real benefit of digital joint monitoring is in vehicle development & testing. For example, a structural load-bearing joint is analysed, and all the conditions mentioned in the opening comments are taken under consideration and a resultant theoretical tightening torque strategy is generated. Before going into production, that resultant theoretical torque would typically be analysed by a series of CAE simulations. In production, it is not uncommon for torque strategies to be fine-tuned by production tooling as new data comes to light from various maturations of development.
It could become a valid part of joint verification that could be subsequently monitored during rugged vehicle test and dynamic load tests that place significantly more stress on the joint components than would be seen during normal driving conditions. It could help reveal any loss of clamp load perhaps due to further bolt elongation or increased surface embedment under such dynamic load conditions at a much earlier stage than what is possible today. Another potential benefit I see with this type of product is that it would complement or corroborate CAE simulation results or highlight CAE input errors.
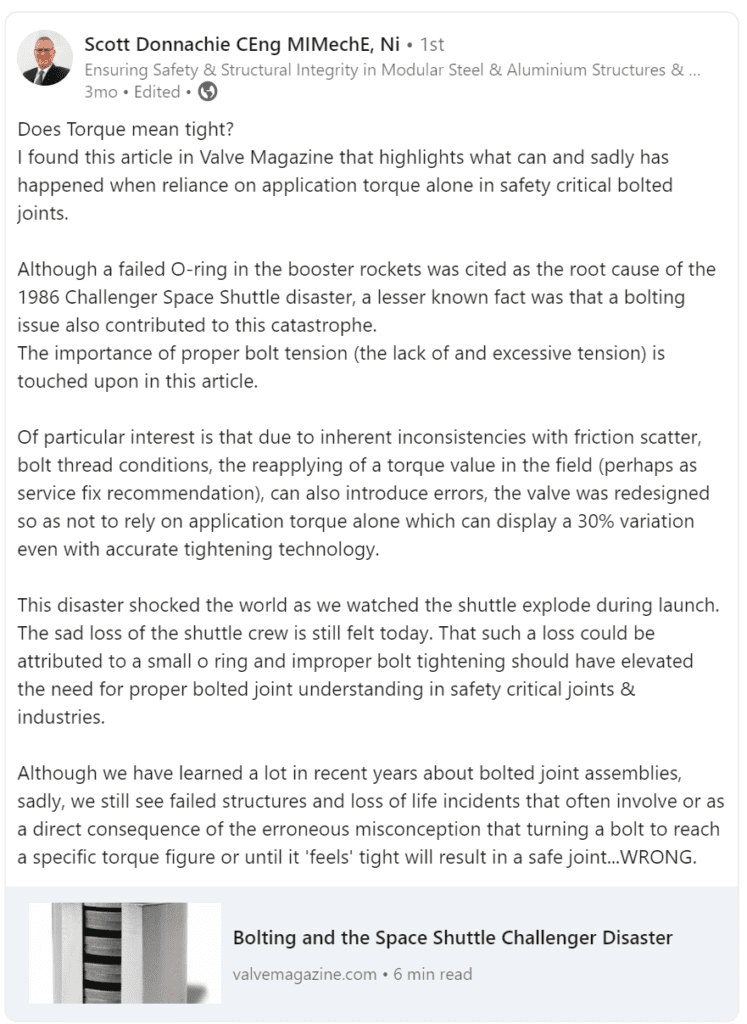
Read more:
- Go to Scott Donnachie’s post on LinkedIn
- Read the Valve Magazine article: Bolting and the Space Shuttle Challenger Disaster
- More on torque in Strainlabs insights section: torque vs preload
- Request a live Strainlabs demo by filling out your name here.
Image: Scotts post on LinkedIn “Does torque mean tight?”