What does a work week for the technical manager at a high-quality niche company within the bolting industry entail?
I have a varied role, incorporating all types of technical matters within Bumax. I work with all aspects of production technique, such as process related trouble shooting and improving productivity and quality. Often when something requires further analysis, I will work with my team on that. I am also responsible for our quality department, Bumax R&D, contacts with universities/institutes and various bolt-related analyses. Bumax work a lot with product and portfolio development. Historically the car industry was central for us but today we are a different company, with a lot more niche profile. In this process our range of products went from two to eleven with the new materials which makes us unique. Last but not least, I work as the technical lead to support our global markets. I handle questions about bolt grades, strength classes and fatigue limits. I guess my work is more commercial than what my title suggests.
How has the market trends and interest for Bumax solutions developed in recent years?
The trend with extending the range of material that we started some 8 years ago has been very successful and the interest is constantly growing for high-grade stainless bolts. Some of our range in this niche is completely unique and those are the products that grow the most. We are still a fairly small company, and it takes time to gain market awareness but we do really see the interest taking off. Last year the standard ISO3506 for stainless steel fasteners added Duplex Stainless Steel – and ISO3506 is almost like a bible for stainless bolts, as it defines everything around it – but at Bumax we started with Duplex some 10 years ago. To me it is clear that we have been a driver in the industry.
What are the key markets or reasons for this development?
Industry-wise the interest in high-grade stainless steel is very broad. Our customers work with anything from airplanes, automotive industry, wind energy, oil platforms, electrical bikes to pumps and valves. A sector that stands out and has started growing rapidly for us lately is also the construction industry both when it comes to for buildings, bridges, tunneling and coastal infrastructure.
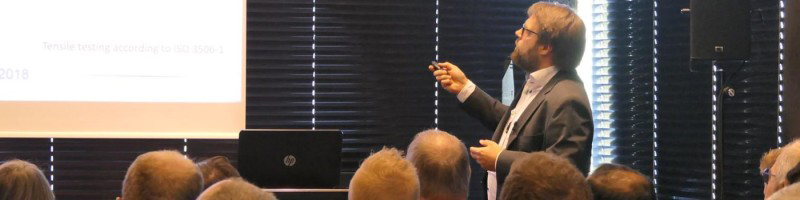
I think the demand for stainless steel is a trend in itself, one important reason being the environmental and sustainability focus. Stainless steel is just about fully recyclable, you can melt it and use it again. Several studies have shown that life cycle cost is better for stainless steel than for galvanized or zinc plated carbon steel. There is more and more research going into this area and the use of stainless steel is increasing globally, a trend that of course is beneficial to Bumax. Our role is also to offer stainless bolting products with quite special characteristics and capabilities. If we take the construction industry as an example – they have a very rigid focus on sustainability. In addition, recent scientific studies (such as the EU financed SIROCO project) clearly state that the construction industry can utilize preloaded assembles with stainless steel (EN1090). Previously the standard in that industry only stated steel for preloaded assemblies, so it has been a hinderance for stainless steel bolted assemblies with no clear testing or proof method for even considering it. The recent changes of course open new doors for us as our bolts have good preloading characteristics. We were also partner several EU-research with the institutes and universities, and a lot of the tests made to confirm viability in construction applications was made with Bumax products.
How do you see Strainlabs solution and potential from your technical perspective?
Well to date virtually no one – independent of industry or bolt brand – can control the preload. The common practice is to torque and have fingers crossed that it is tight. Many times, it is not much more advanced than that. I think that this is why Strainlabs is such an interesting solution and we have been following Strainlabs journey for a while, since our bolts are used for Strainlabs stainless range. As I see it there are many applications where Strainlabs can be used, especially the niche applications where our solutions are used – applications where it will be devastating if preload is lost or where it will take a lot of effort or costs to do maintenance or potentially where a failure means shutting down the entire process. Strainlabs feels to me like a perfectly timed product. I can see how it takes a lot of time and effort to develop a completely new technology. Overall based on how market requirements are developing, there are many applications out there where a combination of high-grade stainless-steel bolts incorporating Strainlabs solution will be highly relevant for our customers. It is a good combination with two expert niche companies securing the best of both worlds – the IoT technology from Strainlabs combined with our high-grade stainless fasteners.
How in general do you see Bumax customers preparing and developing when it comes to megatrends in Industry 4.0 and digitalization?
There are still a lot of industrial companies that have not changed much in practice yet, but we clearly see that there is traction. The wider trend is more visible from the larger industrial players, via investments and specific departments in the last 5 or more years, where effort is actively being directed into the digitalization of equipment, solutions and processes.