Strainlabs Bolts measure their own preload at a regular interval, in its standard version every 10 minutes, for automated bolt inspection. In addition, the bolts have a tightening mode activated for a shorter period for enabling direct feedback on preload development during for example installation. The feature has now been launched in Strainlabs analytical software and demoed live during May at multiple events.
Roger Viberg, Timeless Er HB, has a long experience in tightening technology and maintenance, working for among other Scania for decades and is an experienced trainer in Atlas Copco tools. At Europe’s largest maintenance event “Underhållsmässan” in early June he tested untightening and tightening a joint with Real Time mode activated in Strainlabs Analytics.
Strainlabs: What is your background and experience with bolts in general?
Roger Viberg: I started out in tooling manufacturing in 1976, back then we did a lot of retightening checks with torque tools. In the mid 1980s we started out using strain gauges. Although my focus are the machines, understanding clamp load and preload in bolting has always been an important part. I have seen for example just how crucial keeping track of friction is, in tests with dry vs lubricated bolts we could see that there was a variation of close to 60% in the same joint! Although variation has decreased now with waxed bolts, friction is still a high risk if you don’t have control over it.
Strainlabs: What did you think of Strainlabs preload demo?
Roger Viberg: It was a really good demo, I personally think it would be great to have in any tightening technique courses to spread knowledge and understanding about torque, preload and friction. It is something new to see in real time the preload without having to use an external tooling! I do a lot of training on machinery and bolting with partners. It is so important that the maintenance engineers understand holistically how things relate when they set the machinery parameters – and to understand the machinery they must understand the joints in it.
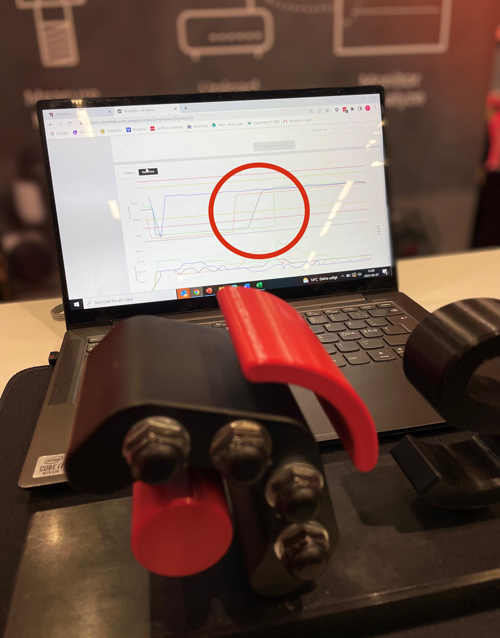
What are your thoughts around the preload insights that Strainlabs System can give?
It is great that now it is possible to not only have the torque-angle measurement but also the preload result in real time. And then the addition to be able to get preload value directly from the bolt over time, and not just at installation, is a great benefit.
Another thing to keep track of would-be friction, it shouldn’t be too low to risk bolt rotation. Friction is kind of like a mantra in the trainings that we do. I say to student’s “It doesn’t matter what torque you tightened with if you don’t know the friction”.
Strainlabs CEO Csaba Madru comments: “The system has been designed to enable predictive maintenance but the insights are valuable in multiple ways including ensuring a correct installation, analyzing what affect preload in real time and over time and in addition learnings and trainings related to design and process”.