Preload monitoring
Torque vs Preload
Definitions
What is torque? What is preload?
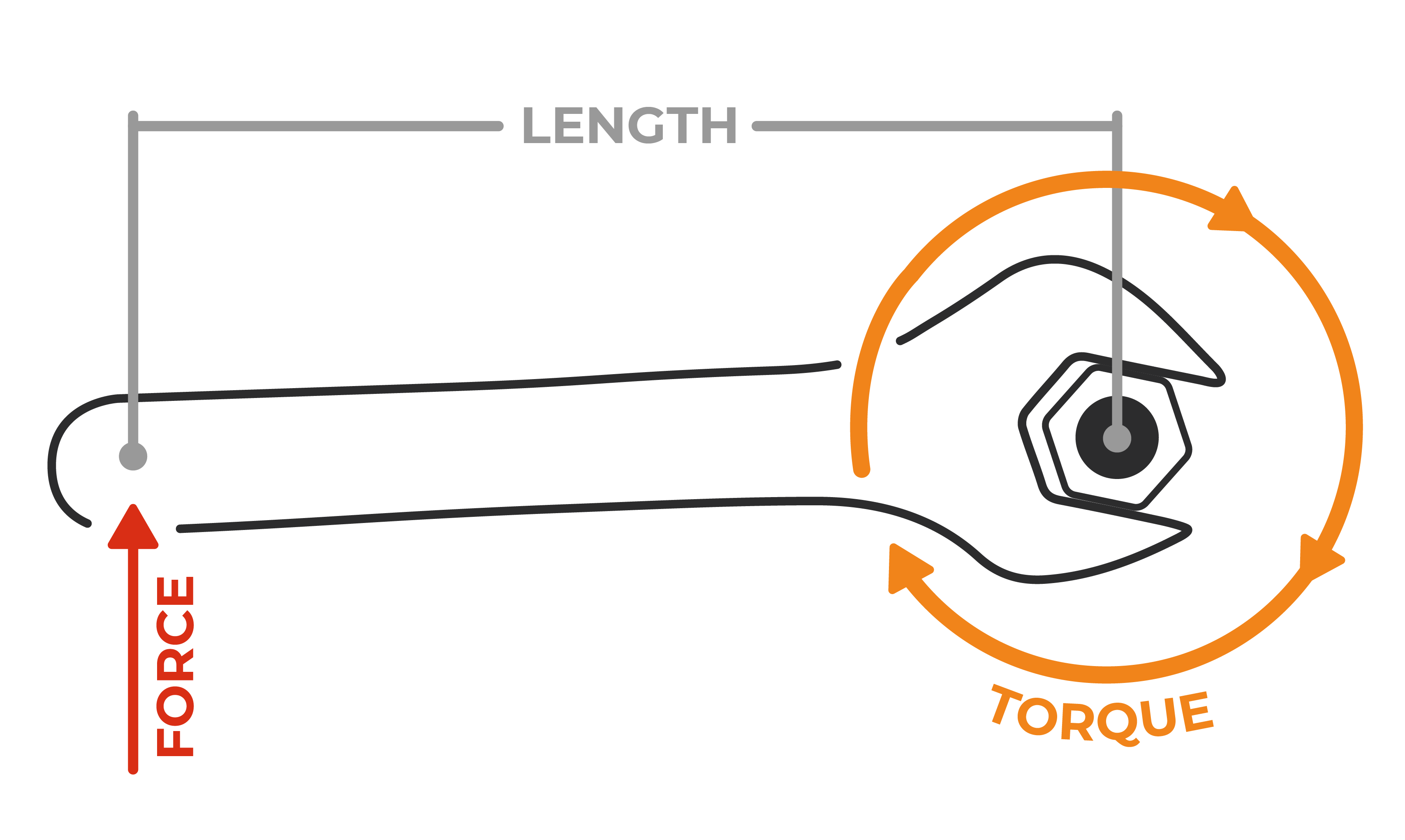
Torque definition
Torque is the length of a lever multiplied by the perpendicular force applied to it. Measuring torque is an indirect way of estimating preload.
Torque (T) = Force (F) x Length (L)

Torque must overcome friction
Torque is the length of a lever multiplied by the perpendicular force applied to it. Measuring torque is an indirect way of estimating preload.
The majority of input torque is needed to overcome friction in the joint.
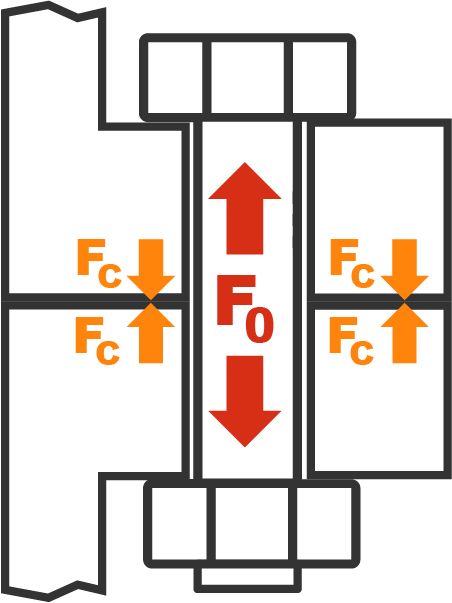
Preload – the axial force in the bolt
Preload is the axial force in the bolt that is introduced by tightening. A preloaded bolt creates the reactive clamping force in the joint. A bolted joint will be challenged by vibration and dynamic loads, thermal cycles and natural settlements, and relaxations in the clamped parts. Therefore, achieving and maintaining preload is critical for the bolted joints functionality.
Achieving and maintaining bolt preload is critical for what external forces and environmental challenges the bolted joint can withstand.
Torque & Achieved preload
The relationship between torque & achieved preload
Due to the reality of the relationship between specified torque and preload outcome, it is difficult to construct a safe bolted joint from a tightening perspective. In strive of ensuring functional preload, joints are commonly over-dimensioned.
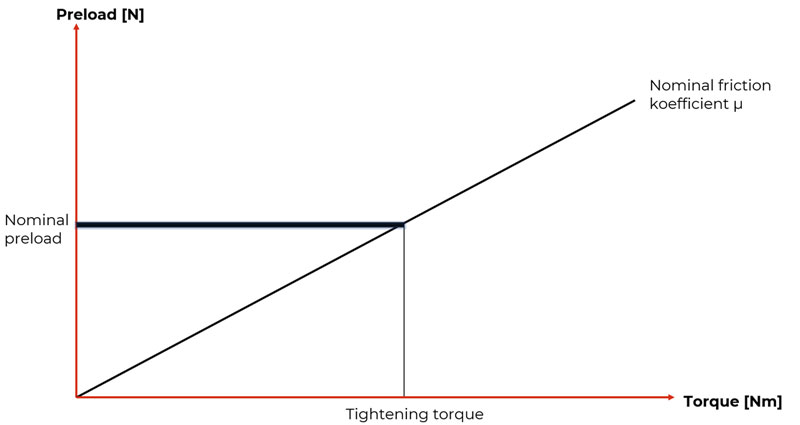
The relationship between preload and torque is linear and determined by the friction coefficient. Theoretically, a specific torque value corresponds to a specific preload value.
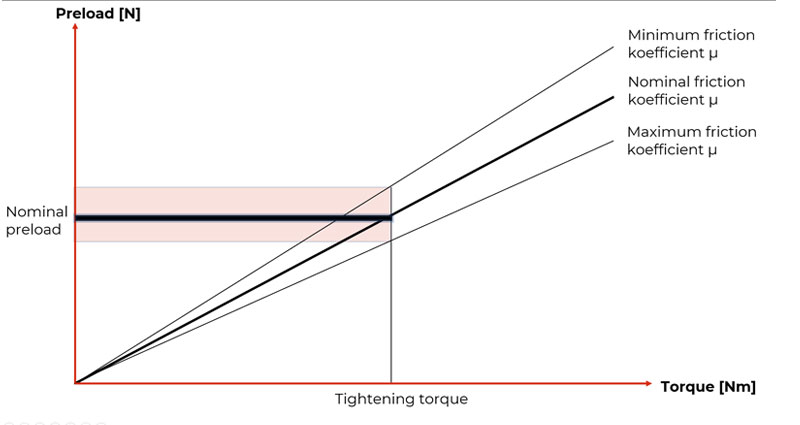
However, the friction coefficient is not a set value, but varies between a min and max level. Therefore, a specific torque value results in a preload value within a range.
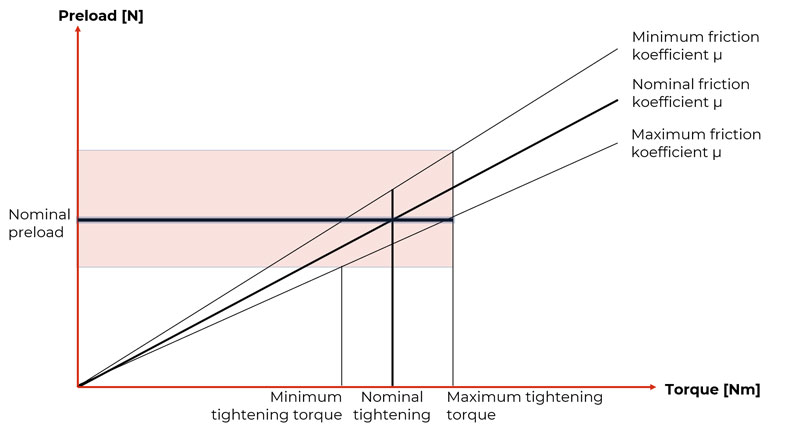
To make matters more complicated, the tightening torque also varies due to tool inaccuracy and the operator. Thus further increasing the variation in obtained preload.
Functional Preload range
What happens if the bolt preload goes below or above the functional range?
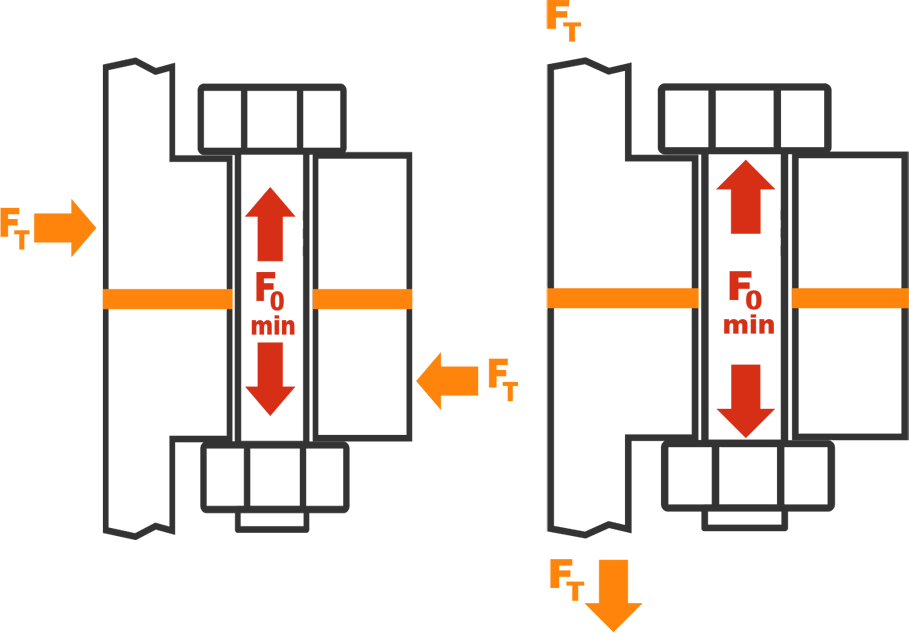
Going below minimal
functional preload risks:
Lost contact (unintentional loosening)
Sliding between clamped parts
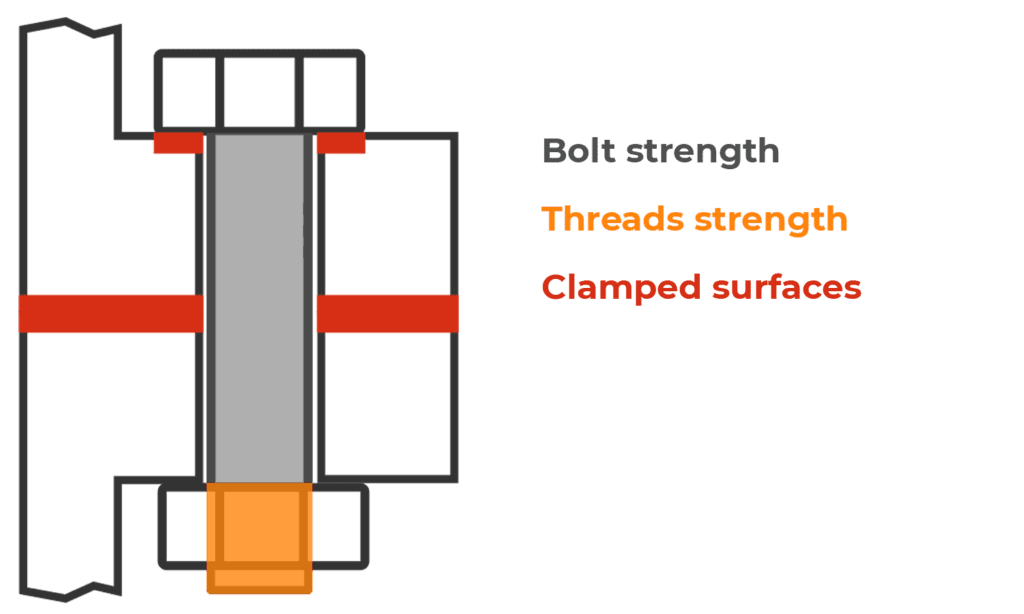
Going above maximum
functional preload risks:
Yielding of bolt (i.e. overstretching), threads or the strength of the clamped surfaces
Bolt tightness
How to know how tight the bolt is?
Since the bolt was invented, mechanical engineers and installation teams have had to rely on torque measuring and performing impractical and manual work – without a lot of accuracy. Examples of such work include:
Measuring torque input
Measuring torque input commonly done at installation for a rough idea of preload, however, as explained above this method normally involves several unknown factors and assumptions which make it difficult to be certain that a functional preload has been achieved.
Torque check inspection
Torque check inspection is made by utilizing a calibrated torque and checking if it “clicks”. If the bolt does not move it is considered okay. The problem is though that the frictional condition could have changed significantly since tightening.
Retightening inspection
Retightening inspection is a more valid inspection compared to torque check, but it means that the tightened bolt is untightened and tightened again. Normally the force required to untighten is checked, to know that the bolt is safe. Untightening torque is often not linear to the tightening torque; however, this is a somewhat more accurate and a reliable method compared to torque check inspections. It can seem a bit ironic to have to untighten (completely loosen) a bolt to know if it is safe.
So how is it possible to know if a machinery relies on the tightness of a bolt? Historically, bolt preload could only be measured under laboratory conditions. Strainlabs preload monitoring solution equips bolts with a preload-sensor that regularly reports preload levels, a solution that for many industrial applications quickly pays off compared to manual torque inspection and maintenance schedules.