Preload monitoring
IoT & Sensor Technology
Digitalization across industries
A sensor is a term for a device which collects and transmits data, a signal and other form of stimuli. Sensors are used in industrial applications for process control, monitoring, and safety. Besides delivering production or asset data they are also defining new business models within digitalization service and site management.
The digital interface of IoT solutions enable modernizing of industrial operations. Sensor data are used to collect data for decision making and productivity development, competitiveness, sustainable improvements and more. Sensors also play a vital role to detect and report properties crucial to health, safety, security and the environment of a process.
A key driver for most industrial digitalization is flexibility in processes that would not be possible otherwise and additionally efficiency related to maintenance and optimization.
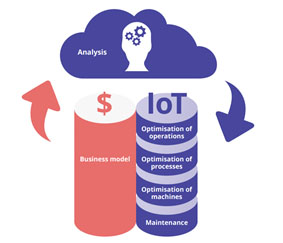
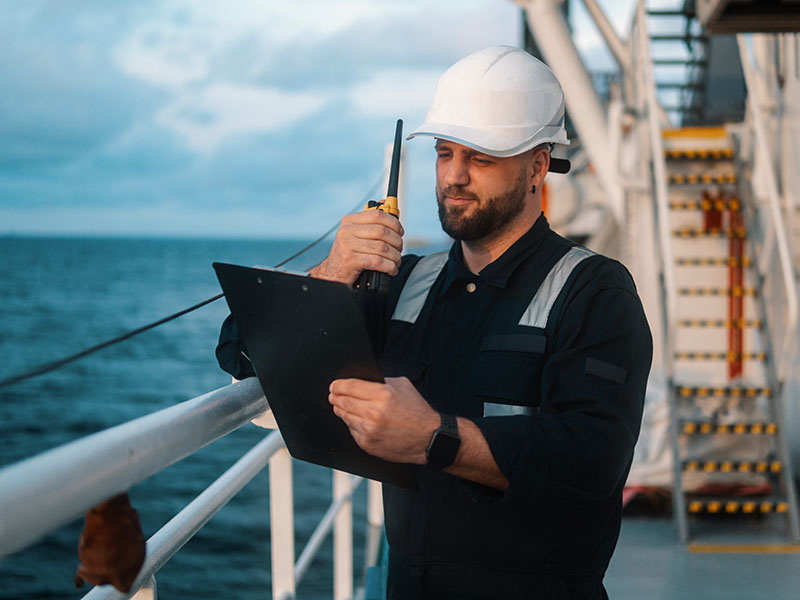
Strategy of the past
- Historically processes and machines would run until they break
- Then industries began implementing planned maintenance by a fixed interval to lower risk of failure
Smart Maintenance through IoT and Sensor Technology
With megatrend Industry 4.0 Remote Condition Monitoring and Condition Based Maintenance are becoming buzzwords, but rightly so. Defining what key parameters to measure, to remotely monitor and to improve unlock maintenance development. Remote inspection and planning is a “low hanging fruit” and highly relevant from an ROI point of view to start a digitalization journey.
At several companies, IoT and Condition Monitoring is becoming its own category within the maintenance setup.
Historically
Run until it breaks
Last few decades
Maintenance by schedule
Industry 4.0
When needed/predicative
Challenges and opportunities with implementing IoT in Maintenance processes
There are some key aspects and considerations when implementing sensor technologies related to maintenance and inspections:
Avoid failures before they happen
The lowest hanging fruit related to Condition Monitoring is the ability to avoid functional failures, they are costly, can be dangerous and further as they are unexpected will take longer to resolve.
Worker safety
Remote monitoring can have a huge impact on for example minimizing exposure to dangerous areas / tasks and only perform them by maintenance personnel when absolutely required. Worker environment and efficiency is increased simultaneously.
Integration considerations
The data from an IoT device need to integrate primarily with existing people and processes, and secondarily with existing technologies and IT platform. Today in general the industry is lacking standards to integrate from mechanical to electric/digital why parallel software may be relevant, especially in a testing phase. Consider if or how the data (alerts and insights) from the IoT device can be incorporated to provide value either by use of existing personnel or via a digitalization / service partner.
Competence and resources
IoT-systems allow remote monitoring of hundreds of industrial machines from anywhere in the world. When regular maintenance / inspections requirements exist praxis, law or regulations relevant and calibrated data can complement the human-based activities. Some IoT systems may require specific competences for analysing data while others have their alert system ready out of the box for use by existing personnel. res
Remote inspections
IIoT sensors enable remote asset condition monitoring. Detect issues and schedule maintenance instead of maintenance at fixed intervals which can mean over-maintaining. Consider the type of equipment you will be monitoring, the data variables (what information you want to collect) and how you could use that data. Simply analysing what happened in the past is no longer good enough and select IoT solutions that supports predictive and prescriptive insights to ensure ROI. The more remote or hard-to-reach location, the more value from being able to have the data regularly and automatically.
Manual vs digital inspection/maintenance
A key difference between manual and digital inspections is that they can be automized with a certain interval. The digital regular updates on equipment condition reduce need to use labour for manual inspections by praxis, or as required by regulations. Value creation occurs when productiveness increases due to leveraging the knowledge and insights from data to support decision making. Condition Monitoring can increase production flexibility and worker responsiveness.
Sophisticated analysis
When selecting an IoT solution ensure it is built up to enable more advanced learning in the future. Machine learning can improve diagnosis and learnings, but will require a significant amount of data from your application before it can give value. It is recommended to start small with an IoT pilot or test project - but ensure that the test can grow in scale and value. Examples include analysing data from multiple machines and implementing AI or similar. With large data predictive models can be made. Strainlabs Analytics has been prepared for AI development, something that is made possible once preload data has been accumulated.
Strainlabs Preload Monitoring VS other types of Condition Monitoring
Common types of monitoring include vibration, temperature, levels of CO, abnormal reduction of oil level. What separates Strainlabs preload monitoring is that the sensor is also an integral part of the mechanical structure [link to Strainlabs Bolts], not a separate sensor on the side.
Mechanical failures are a recognized risk in any operation and bolts are commonly an exposed part of the structure. Knowing what to measure and how to interpret data is a common challenge, including how to put the data insights to use. With Strainlabs we make the data actionable from day one with clear alerts and data visualization related to functional preload levels. Condition monitoring reduces the risk of failure and allows teams to order parts in advance, schedule manpower, and plan additional repairs during a downtime.
Contact Strainlabs today to learn how we can help you get started with IoT for Condition Monitoring and Condition Based Maintenance through Preload Monitoring.
The digital interface of IoT solutions enable modernizing of industrial operations. Sensor data are used to collect data for decision making and productivity development, competitiveness, sustainable improvements and more. Sensors also play a vital role to detect and report properties crucial to health, safety, security and the environment of a process.
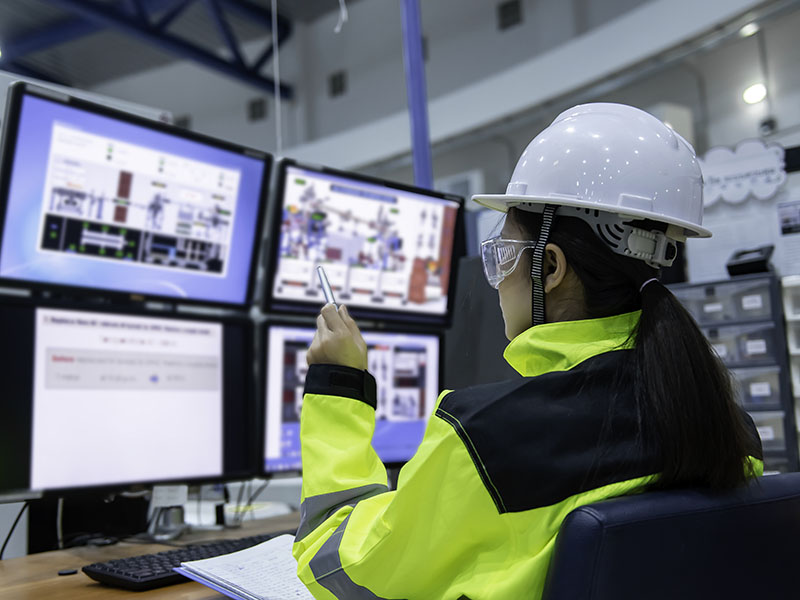
Efficiency and optimization are key advantages with industrial digitalization. Another key driver is to enable / increase flexibility that would otherwise not be possible.