How did the term IndTech come to be?
The strategic innovation program PiiA enables funding for industry projects from Vinnova through open calls and strategic projects. The program has so far enabled financing for industrial digitalization, development and innovation to a value of 1 billion SEK. It was some 10 years ago that we for the first time thought that there is a lot of talk about FinTech, MedTech and other tech terms and we found it strange that nobody said IndTech. A few years ago we started a more strategic approach to establish IndTech as a term. The Swedish industry has a lot of installed base equipment with a lot of operational lifetime left which we think should be seen as an asset to digitalize rather than a problem.
How would you explain what IndTech is all about?
Industrial Sweden is to a large extent already computerized, and a lot of the success of the Swedish industry we see today is thanks to the computers that runs that equipment. If you go into a large steel plant or a paper mill there are rows of computers already set up. IndTech must take off from this starting point and bring together the possibilities of connecting operational technology (OT), information technology (IT) and new digitalization phenomena such as cloud, AI and IoT. The new technologies are globally available – a new robot from ABB, control system from Siemens or a software from Microsoft – everyone can buy it. Competition in the next phase is about taking the new technology and apply it to the industrial reality in an efficient and relevant way. Sweden has a great starting point and our ability to progress and develop in this area will affect Swedish economy and competitiveness going forward.
How do you see sensors and IoT solutions as part of this development? For the industry, the sensors are the starting point of getting the data that enables digitalization. In many industries we are used to measure quite a lot of things, but we are far from having all the data that would be valuable available to analyze. Solutions such as Strainlabs IoT bolts are interesting since it so clearly ties into predictive maintenance. I think such IoT solutions have a great potential forward, to be able to measure in new ways and further to analyze that data cleverly to predict better and understand better. From PiiA’s perspective we plan an upcoming study on the new state-of-the-art Industrial IoT solutions, with the aim to inspire and challenge to contribute to development. The term predictive maintenance has been around for quite a while, but there are new IoT technologies to enable the relevant data and they create new prerequisites. The data from those solutions enable new possibilities for services and business models.
What would you say are the current challenges for IndTech to overcome?
In the large technology shift in the 90’s with modern automation I found that when business leaders where inspired and challenged by others it supported change. I think this is a key need now again. In general, the basis to move towards digitalization for industrial companies is three things – IoT, computing capability (cloud), and capability to perform data analysis. If you have that you have a platform to build on, of course not all analysis and setup needs to be done in-house, but you should have the basic structure.
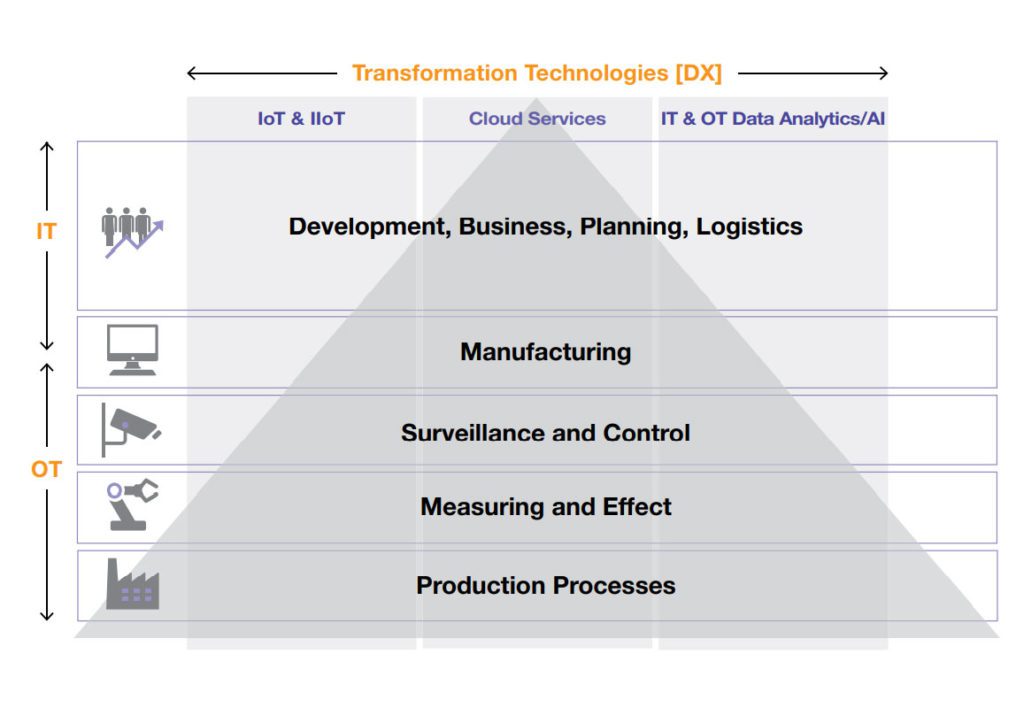
If I refer to what we call the automation pyramid we describe the two separate IT and OT (operational technology) layers. Then you have three key transformation techniques:
- IIoT/IoT is the application platform for automation and the methodology for achieving data
- What we recommend is to ensure you have computing force, typically with a cloud strategy.
The third layer is analysis of industrial data from the IT and OT layers.
Within Swedish IndTech have a need to enable analysis due to lack of access to data. Companies tend to hold on to their data. We need more exchange and common learning otherwise we will miss a lot of potential values to learn from one another which is needed to enable the shift. Currently we see that data is being shared more openly in public sectors such as banks and authorities, that is something we need to see in IndTech to reach the full potential. I hope we will see more companies that helps compare and benchmark best practise for IndTech to challenge and inspire progress.
There are quite a few IT and OT systems and new software to navigate between as an IndTech solution. How do you see this?
The industrial digitalization framework needs to become global if we want our value chains to be connected. A lot of work is ongoing nationally and internationally since standardization is crucial for interoperability. At PiiA we are just about to finalize a 4S project targeting standardization and connecting Swedish research and development within IndTech with the large international standardization projects such as ISO and IEC. In the summary report we conclude that this technology shift is just as much a revolution as the previous industrial revolutions. How all the pieces of the puzzle that is up in the air will fall into place we don’t know yet, which can be frustrating. It is a heavy part to set up the framework around a new technology – and it needs to work long term.