As all widely used components, bolts are highly standardized. One of the most important aspects of bolt standardization is the strength of a bolt.
- ISO 898-1 is the international standard that defines the mechanical strength for metric carbon steel bolts.
- ISO 3506-1 is the corresponding standard for metric stainless-steel bolts.
In simplified terms the strength of a bolt can be considered in three parameters:
- The ultimate tensile strength, which is the maximum load the bolt can withstand before it breaks.
- The yield strength, which is the maximum load the bolt can withstand before it is permanently deformed by 0,2%.
- And finally, the proof load which is the highest load a bolt is intended to withstand without any permanent deformation. The proof load is roughly 85%-95% of the yield strength.
Partially vs fully threaded bolts
Strainlabs Bolts are manufactured from standardized bolts for highest compatibility possible with the existing environment. In order to comply with the ISO standards, the load supporting capacity of Strainlabs Bolts must be fulfilled and a fracture during tensile testing must occur in the threads or shank – more information in this article. Since Strainlabs Bolts are fitted with a sensor, a small cavity needs to be machined in the bolt which results in two different scenarios depending on the thread design:
1) Partially threaded bolts
Partially threaded bolts (normally ISO 4014). Since the load supporting cross section is larger in the shank than in the threads even after machining the cavity for the sensor, the load supporting capacity of the bolt is still maintained and the threads are still the weakest part of the bolt. For small bolts sizes, such as M10 and M12 a small decrease in load supporting capacity of up to 13% can be detected. However; the standard is still met. For bolts of size M16 or larger, no loss of strength has been identified in tensile testing.
2) Fully threaded bolts
In this case the load supporting cross section is inevitably reduced when machining a cavity of any size, which, in its turn lead to a reduced loadbearing capacity. Since the sensor cavity is the same for all bolt sizes, the effect is smaller the bigger the bolt is. It is also possible to compensate with a higher bolt class for example. Strainlabs has made calculations to determine the load supporting capacity of the bolts and can assist in testing if required.
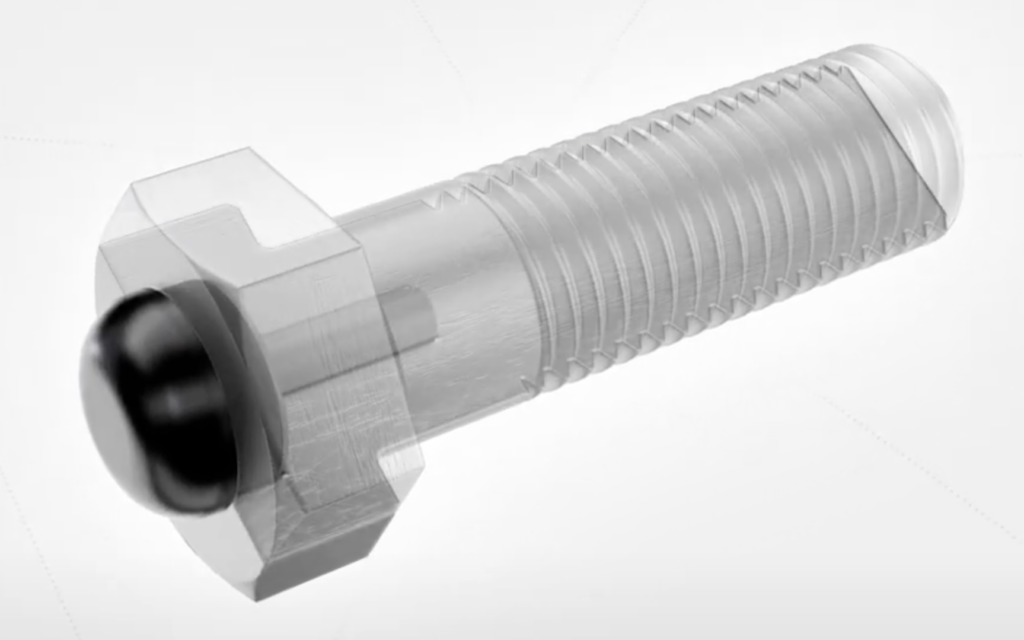
Meeting ISO requirements for entire range
Meeting proof load requirements according to ISO standards is a vital property as it enables the use of standard bolts without altering its mechanical properties. With our newly launched additional sizes of M22-M27 our standard range consist of bolts in sizes M10, M12, M16, M20, M22, M24, M27 in steel (8.8, 10.9 or 12.9) and Stainless steel (A4-70, A4-80 or Bumax® 88, 109) or special alloys.