1. How does your average work week of helping ABB’s customers realize Industry 4.0 and digitization look?
My main work task is to translate digitalization into value for the customer. The digitalization is worth nothing on its own – it only generates more data. But if you can use the data for a result that can be translated into a recommended action then you can begin to capitalize on digitalization and improve a process. I work with new methods and strategies for maintenance and how to optimize results from the available data. Supporting companies in how to change the activities is also key, if a maintenance team continues just like before after a digitalization initiative, then there has not been any improvement. In the end my work is quite pedagogical and almost philosophical around digitalization. We try to make digitalization more human – what does this particular data mean to you, your worries and pain points? We avoid hiding behind the technical specifications of what we can help customers, industries and even the society with and be specific about how sensors can help in the daily life and work.
Our customers are basically the large process industries in Sweden meaning mechanical, paper, mining, and steel industry – this is the financial backbone of Sweden’s economy and a key part of our export trade. The customers have huge complex sites, and our job is to help them achieve better control and predictability. The offering is condition monitoring, but the outcome is not only the status of the machinery but also other valuable information such as energy consumption, which is important to analyse and work with to achieve the CO2 neutral industry and society we are aiming for by 2050.
2. How does the typical journey towards industrial digitalization work for ABB’s customers?
We almost always start with education and a pilot in some form so that the relevant team can get used to the technology and understand how to interpret the data. Once the team is comfortable with that a larger installation or complete digitalization journey can be started – but then it is very key to also develop the activities and what changes simultaneously to be done to maintenance routines in terms of interval and so on. We secure the value of the digitalization since the worst outcome of a new project is getting a lot of data that is not used and keeping the same routines as before. But it is a process to learn how to best use and get value from new technology.
3. What are the most prominent trends in industrial digitalization today?
Looking at the process industry in the first trend that comes to mind is the importance of maintaining a competitive edge, since competition is increasing more rapidly with digitalization and automation the companies will need a completely new competence in-house to manage this development – expertise is needed in many different areas which subsequently is difficult to recruit and would cost a lot of money. This in turn creates the need for a closer collaboration between the suppliers and the customers – since the supplier then can offer important competences needed for implementing and getting value out of the technology. It turns the relationship into more of a partnership than a buyer-seller relationship. A key factor in allowing this relationship is sharing of data to the supplier so that we can support with the relevant expertise.
A second trend, looking specifically at the paper industry where we have a high average age of perhaps around 54-57 years for employees. What happens when they are due for retirement? In their work they have developed an expertise that is nearly impossible to transmit to other individuals, and the industry risks losing it. The personnel must be renewed of course but also the suppliers will need to come in and support the companies in a partnership relationship, sharing and analysing data so that the knowledge becomes available – even from a distance and knowing the status of the components and where to spend maintenance time and resources.
A third trend that comes to mind is the lack of time. Data does not help with anything if no one has time to review it! Therefore, analysing data becomes outsourced and suppliers like us can help to identify if machinery acts in a non-normal way, meaning identify it before something breaks since nothing goes from perfect condition to failure directly. The job becomes to detect which systems and components have a “health condition” so we can act before breakdown. Often, our customers’ need help to understand data and commonly they also need help to monitor the data. This also relates to that Sweden is a high-cost society and it is not feasible for each company to have a lot of personnel in this area with the different types of expertise involved if they instead can use a supplier who in a cost-efficient manner highlight when it is time to act on.
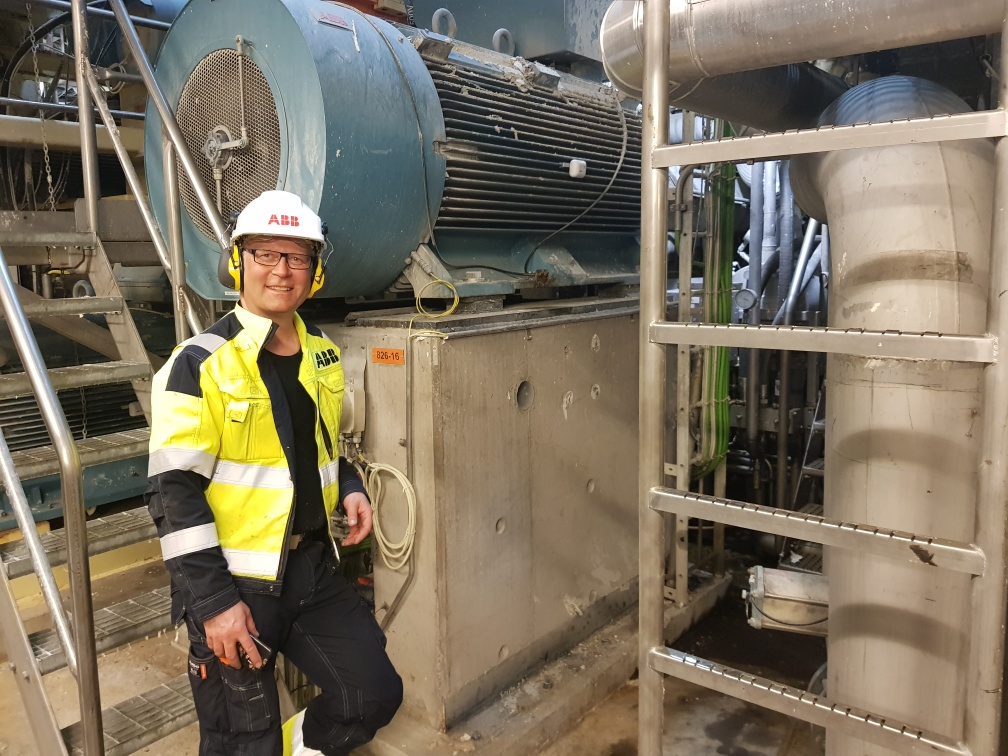
4. How do you see Strainlabs bolt preload monitoring solution and its ability to provide value to industrial companies?
Strainlabs is a very interesting company within our growth hub SynerLeap Powered by ABB. In many industries bolts have quite prominent inspection routines and often, they need to be retightened. Let us make a thought experiment. Say you have a service engineer in your plant, and he has a task to inspect 40.000 bolts. Each bolt takes 2 minutes. He inspects all bolts and finds that 10 of them needed to be retightened which he does. How much of his time worked did create value for the company? 20 minutes of 80.000 minutes gives 4 minutes per thousand minutes (0,4%)! What if he instead knew which bolts that needed retightening so he can spend basically all the other minutes creating value on other service jobs as well?
I think this type of thinking puts things in perspective. A lot of what industrial companies spend time on maintenance wise are things that they really must do because their future depends on it. What if a main beam in a factory hall is not tightened correctly and falls and stops production? But how do we know that it was that bolt we needed to fix? Strainlabs condition monitoring provides a lot of value in terms of where to focus maintenance efforts.
Another key value is personal safety. How does the environment where the bolts are located look when inspection is due? Are there electricity, hot surfaces, rotating equipment – every minute spent in an exposed environment is an increase in risk for accidents. If you only had to go in and retighten 10 bolts – how much less time was it that for your personnel to spend exposed? Human lives are impossible to put a value to, and that is not a benefit to underestimate with Strainlabs solution.
5. How do you see Strainlabs and preload monitoring compared to other methods within condition monitoring?
Relevant to consider about condition monitoring as I see it there are two types – the basic type is that you know what part or machine has an error and needs inspection, the other category is when you get information to be able to learn from the information and judge what is causing the error. All condition monitoring methods aim to judge the health of the operation. It depends on the component which parameters are relevant to measure to define the health of it. It is important to review the right things. When it comes to bolts the aim is through torque achieve the desired preload. If the preload changes – what has occurred? What is it in the environment that cost a preload change? There are many causes – thermal cycling, vibration etc. it is important to find the cause of the change, and then it is also possible to work around it and find a solution for it not to happen again. Something that is much easier when you have all the data combined.