Safety and security routines at amusement parks are rigorous, involving daily checks and tightly reoccurring in-depth controls. EN standard 13814 and local regulations dictates maintenance routines in details which must be completed before each attraction can be open for the day. In a unique collaboration to explore the advantages of remote monitoring in amusement park applications, the maintenance team at Gröna Lund has together with Strainlabs engineering performed an all-weather installation on Nyckelpigan rollercoaster.
Strainlabs Bolts installed on Nyckelpigan rollercoaster
Bolted joints are increasingly common for joining parts together at ride suppliers. This has led to that the time required to inspect and retighten bolted joints represents a substantial portion of maintenance time spent during each maintenance cycle – “I estimated that up to 35-40% of our inspection and checking time spent is now related to bolted joints” explains Peter Andersson, Ride Safety Manager at Parks & Resorts Scandinavia AB. Strainlabs Bolts were installed in Gröna Lund as part of a learnings and exploration partnership in how remote preload monitoring can complement existing maintenance and safety routine in these types of applications.
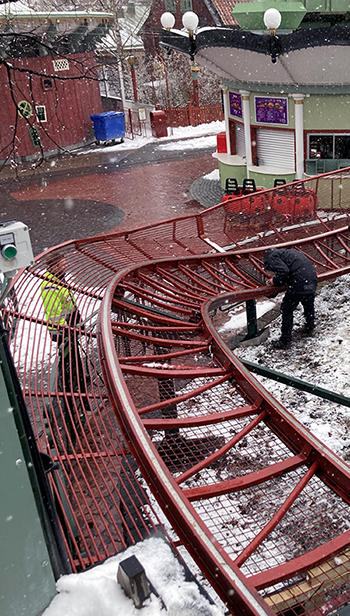
Installation data
Location: Gröna Lund, owned by Parks & Resorts Scandinavia AB.
Application: Rollercoaster tracks on Nyckelpigan.
Implementation: Strainlabs Bolts installed sending data via radio signal through Strainlabs Router and presented via Strainlabs Analytics.
Condition: Installation during the period June 2022 – August 2023 so that Strainlabs Bolts were exposed to all seasons – including Swedish winter conditions.
Outcome and learnings
Automated remote preload measurements add safety measures both in ensuring correct installation from start and as a cost efficient way to add cadence to inspection of bolts.
Erik Göranson, Technical Manager Rides & Games was responsible from the installation at Gröna Lund lists key learnings and values identified during the installation:
- The ability to check quite directly through software if the torque tool used was accurately calibrated, from the office, adds a safety dimension to the job.
- It was very interesting to see, in preload data, how tension can vary with different external factors such as temperature.
- The ability to get an indication or alert when an individual bolt needs attention outside of its regular “maintenance window”.
- To with higher frequency digitally check the bolts that are hard to access.
“We have begun discussing our learnings with ride manufacturers as any broad implementation requires their involvement” concludes Erik Göransson.