This article entitled “The railway industry has gotten its own crystal ball: Smart bolts predict the need for maintenance” was originally written and published in Swedish by Nordic Infracenter – view original article in Swedish.
The Swedish railway system is in dire need of maintenance, compounded by a significant labor shortage. Now, the Swedish innovation company Strainlabs has developed a predictive maintenance system that aims to save time, effort, and money.
Strainlabs, with Sales Manager Gösta Rydin, is driving digitalization in the railway industry alongside its customers. Strainlabs refers to their technology as the “Internet of Bolts,” which is exactly what it sounds like. By equipping critical bolted joints with sensors and communication equipment, following the principle of the “Internet of Things,” the condition and maintenance needs of each bolt can be diagnosed. This product, which holds a global patent, was launched in 2022 and is now used in various switches in the Swedish railway network.
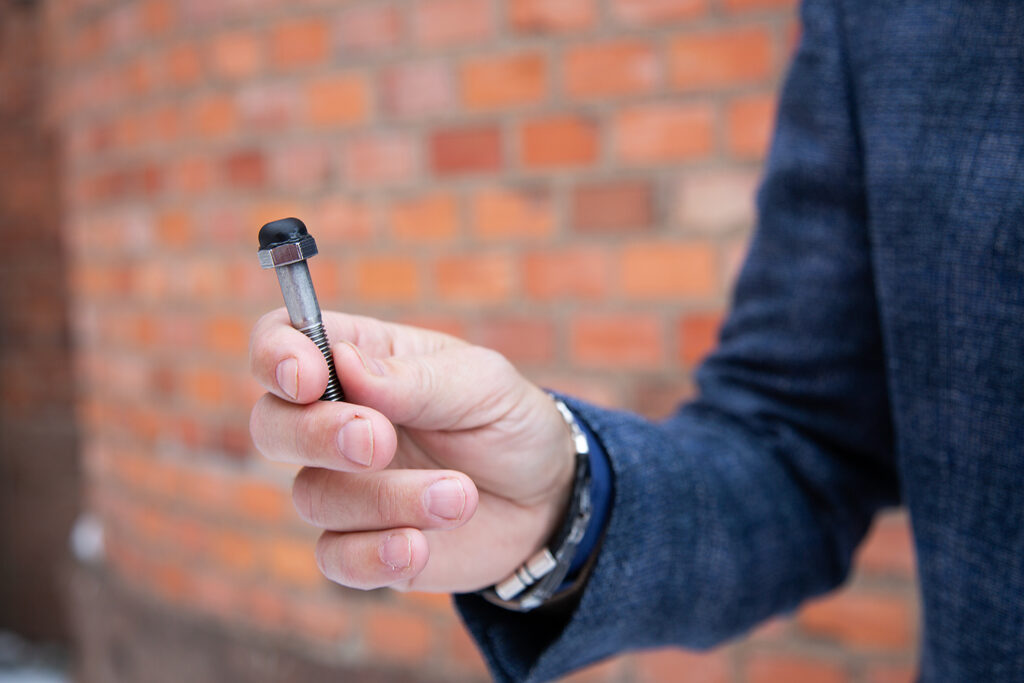
“We have an agreement with Vossloh, who have integrated our system into their switches. We have also recently entered into a deal with Railway Metrics & Dynamics. Being at the forefront of digitalization is a priority for these players, and we are, of course, delighted that they have chosen us as their partner,” says Gösta Rydin, Sales Manager at Strainlabs.
Measuring with Light
Practically, the process works like this: Clients send their bolts to Strainlabs, who then equip them with a sensor package including battery. According to Gösta Rydin, this process does not affect the bolt’s quality or strength. The bolts can then be used in for example, switches, fishplates, or signalsystems.
“At the moment, we can equip bolts from M10 up to M27,” states Gösta Rydin.
The technology is based on a unique measurement method where the sensor monitors the bolt’s status relative to its pre-tension by measuring light. If the bolt begins to loosen or break – for instance, due to material settlements, vibrations, or thermal impacts – the change in light intensity inside the bolt is measured and translated into increased or decreased force.
The bolts “wake up” according to a set, frequent time interval, providing the client with extensive data over time. The signal is sent to a router installed along the track, and the router then forwards data from each bolt to the customer, who receives the information in Strainlabs’ software. Strainlabs customers can set their safety margins in the software and use the incoming data to monitor the bolt’s status, predict maintenance needs, and allocate resources precisely when and where needed.
No Surprises
The advantages for a stressed railway industry are numerous, says Gösta Rydin:
“As it stands, maintenance is currently carried out according to a fixed plan, based on expected occurrences. This often leads to expensive and time-consuming maintenance which is unnecessarily while it also risks missing critical bolts that have actually loosened or broken prematurely.”
The solution makes it easier to manage when the personnel are under pressure. From a societal perspective, the technology also has the potential to contribute to higher utilization of the tracks.
“The battery in the Strainlabs Bolt is designed to last for a measurement every ten minutes for over five years. It is a very robust solution. The sensor is also prepared for various AI solutions that can further increase the benefit to both clients and society,” says Gösta Rydin.